Computer controlled microscope stages enable high resolution digital microscopy. PI offers several drive concepts to provide precision motion to move samples or objectives in XY and Z. Direct-drive linear motors and voice coil motors are used when long travel ranges are required. When sub-nanometer resolution is required, for example in Super Resolution Microscopy or AFM, piezoelectric microscope stages offer the best performance, allowing researchers to create higher-quality images faster. Z-Stages and collar piezo objective positioners are used for 3D imaging (Z-stack acquisition), deconvolution, and fast focusing applications.
PI's optical-axis Z-positioners typically achieve 10 times higher precision & focusing speed than conventional motorized Z-axis positioners. Controllers are equipped with high-bandwidth digital and analog interfaces for extremely fast response and compatibility with all major image acquisition packages, such as Metamorph, µManager, etc.
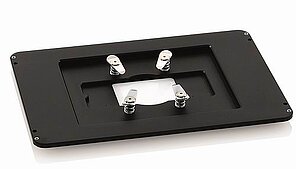
For long travel positioning, highly stable ultrasonic-ceramic motor driven microscope stages are available. These self-clamping positioners provide significantly better long-term stability compared to conventional motor drives.
Check out PI's microscopy blog articles and download the Products for Microscopy and Electron Microscopy catalogs for more information.
Voice coil motors and piezo flexure drives provide high dynamics, velocity, and accuracy - ideal for fast focusing applications such as microscope lens positioning / scanning. These high performance Z-nanopositioning mechanisms can move microscope objectives with nanometer and sub-nanometer resolution and high speed, typically one order of magnitude higher than conventional motorized focus stages.
PI provides voice coil focus nanopositioners with up to 7mm (7,000µm) travel and piezo lens positioners with up to 2000µm travel. For longer travel ranges, piezo motor stages and linear-motor drives are available.
Many of PI’s piezo motion controllers are compatible with major image acquisition software packages to provide high performance images for deconvolution microscopy, Z-stack image acquisition, and other super-resolution techniques. Settling times are typically in the low millisecond range. High guiding precision is achieved with frictionless, computer optimized flexures. Optical encoders and capacitive sensors guarantee sub-nanometer precision in closed-loop operation.
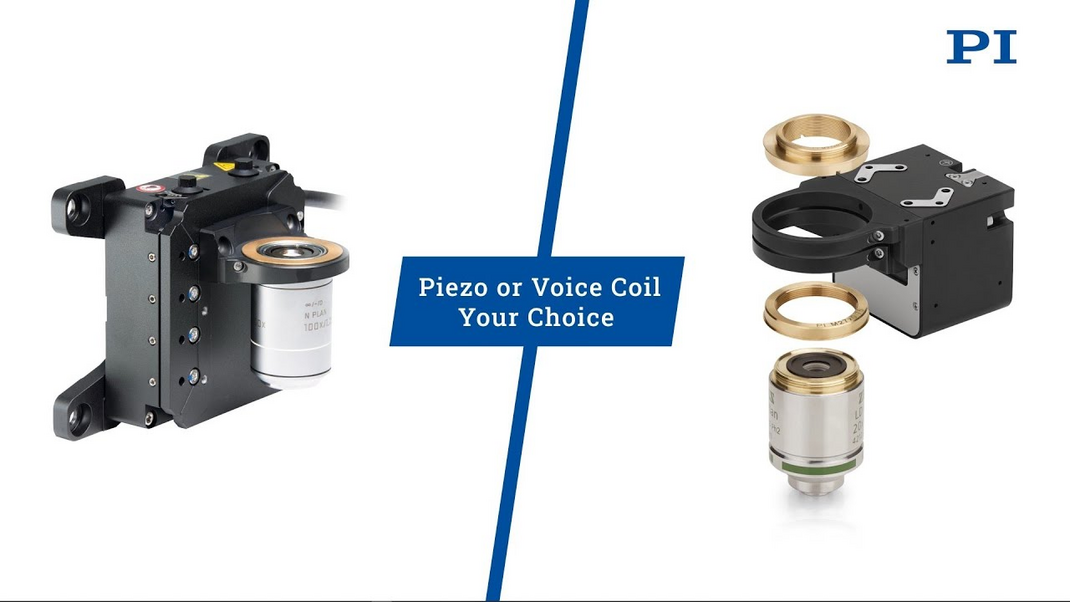
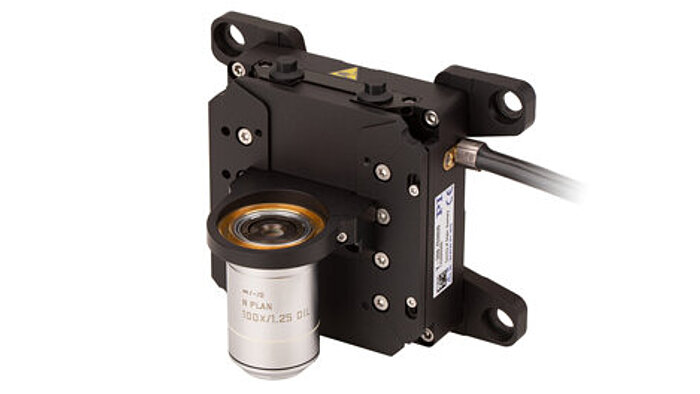
V-308 Fast Nano Focus
Voice Coil Scanner, 7mm
- 7mm motion
- Voice coil linear motor
- Adjustable Z-counterbalance
- Millisecond settling time
- 1nm sensor resolution
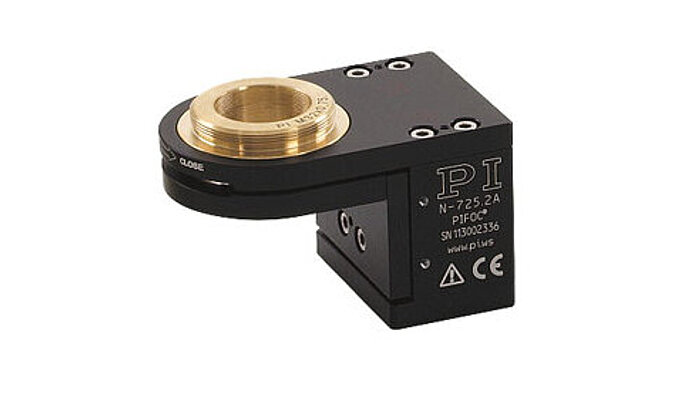
N-725 PIFOC® Fast Piezo Nano Focus
2mm, PiezoWalk® Motor
- 2000µm motion
- PiezoWalk® motor, self-locking
- Package with controller
- Millisecond settling time
- 0.5nm sensor resolution
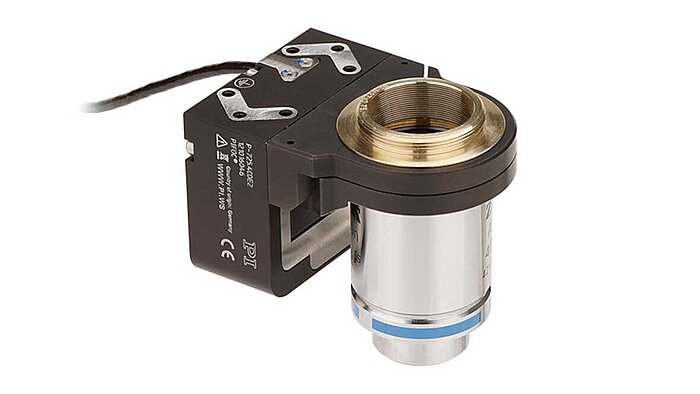
P-725 High Performance Piezo Focus Scanner
Up to 800µm, Sub-Nanometer Precision
- 100, 400, 800µm motion
- Combines higher dynamics & longer travel
- Millisecond responsiveness
- Ideal for autofocus, metrology, pathology
- New high performance controller
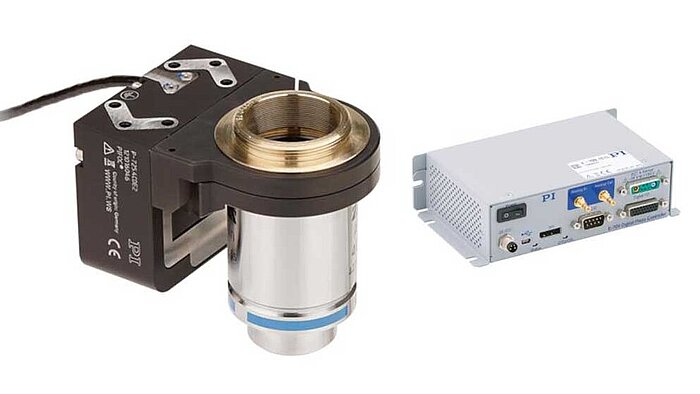
P-725 Piezo Focus Scanner Package
Economical Package with Controller
- 100 and 400µm motion
- Complete with digital controller
- Millisecond responsiveness
- Ideal for autofocus, metrology, pathology
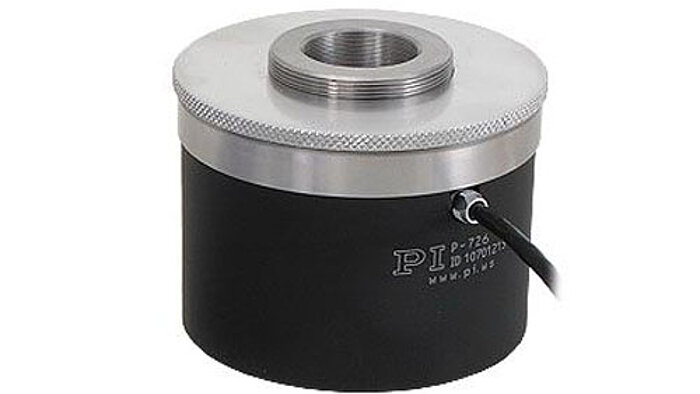
P-726 PIFOC® Fast Piezo Nano Focus
100µm, High-Stiffness, High End
- 100µm motion
- Ultra-stiff for heavy objectives
- Millisecond settling time
- Enhanced focus stability
- Compatible with imaging software
Application Note
The P-726 provides the highest stiffness and fastest response time with heavy objectives.
An application of the P-726 with the E-753 digital controller is described in this article “Remote refocus enables class-leading spatiotemporal resolution in 4D optical microscopy”, where also the U-780 XY microscope stage and the P-737 Piezo-Z stage were employed in the test setup.
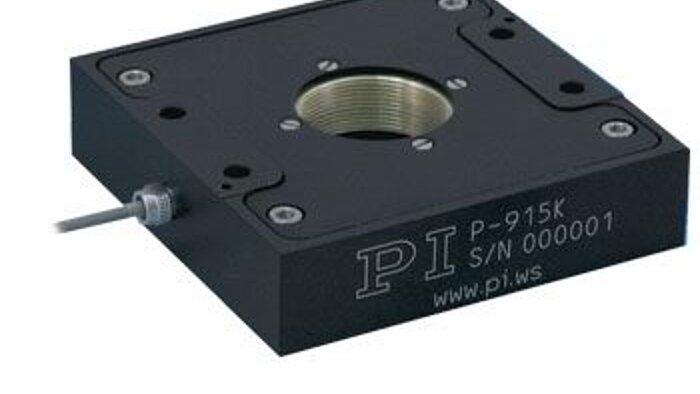
P-915KLPZ Piezo Z-Objective Scanner
Low-Profile
- 75µm motion
- 15mm height, 60x60mm footprint
- For objectives with W0.8 x 1/36'' thread
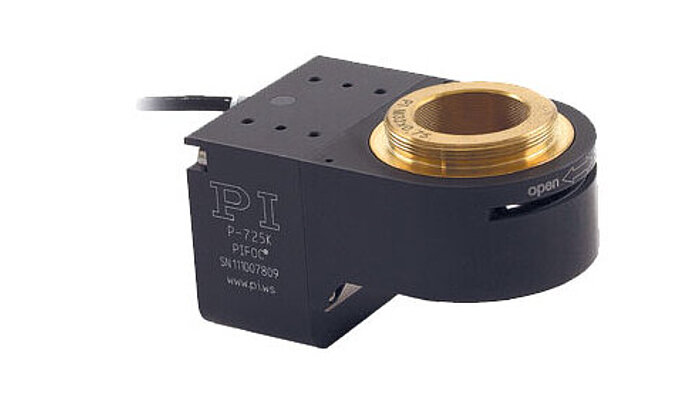
P-725KHDS PIFOC® Objective Scanner
400µm For Heavy Objectives
- 400µm motion
- Higher stiffness for faster response with heavy objectives
- Millisecond settling time
- Enhanced focus stability
- Compatible with imaging software
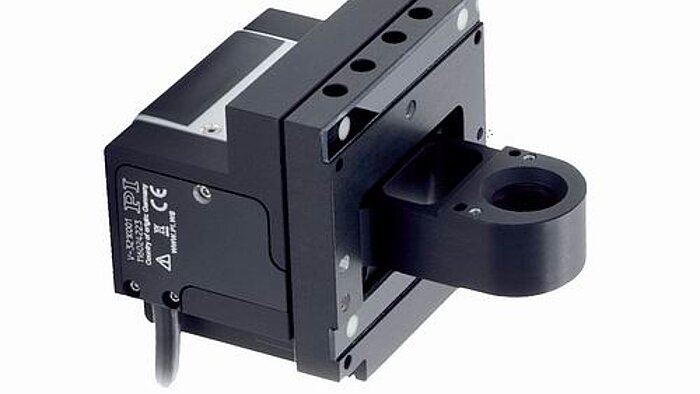
Voice-Coil Fast-Focus System
This custom autofocus system is driven by a PIMag voice coil motor. PI also provides the controller, alignment tools and routines to improve the assembly precision of the payload.

P-721KTPZ PIFOC® Nosepiece Nanopositioner
Move the Turret instead of One Objective
PI has designed a number of custom “nose piece” nanopositoners. The high stiffness of piezo ceramics makes it possible to dynamically move the complete microscope turret instead of one objective at a time.
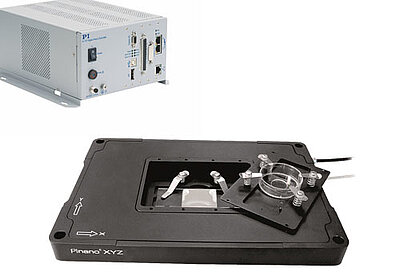
PInano® XY and XYZ piezo nanopositioning stages are designed to mount on manual or motorized microscope stages. They can accommodate slides or other inserts.
Digital Control: The PInano® packages include a digital servo controller (not to be confused with an analog servo with USB interface) which provides higher performance (linearity, dynamics) than conventional analog piezo controllers and allows parameter changes to adapt to different load situations to be made on the fly. In addition to USB and Ethernet interfaces, an analog 0-10V interface is also installed – convenient to use with many existing instruments providing analog outputs.
Piezo Resistive Sensors (PRS): Based on high resolution semiconductor strain gauges, often used in AFM’s, they provide a very high signal to noise ratio and low noise.
Capacitive Sensors: Non-contact, direct-metrology sensors that measure the gap of a moving platform against the static frame and provide the highest linearity and very low noise.
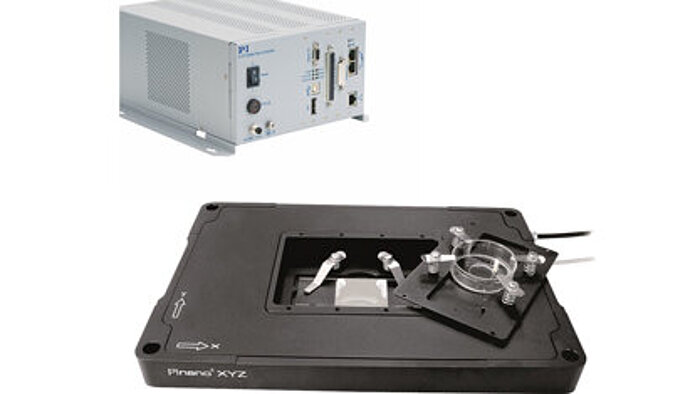
P-545 PINano® XY/XYZ Microscope Stage
Package with Digital Controller
- 200µm motion
- Nanometer resolution
- Easy integration in microscopes
- Sensor choice: Piezoresistive (PRS) - lower cost; Capacitive - higher linearity
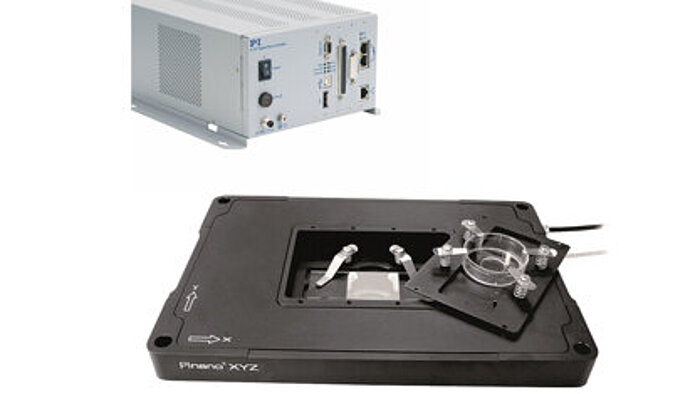
P-545 PInano® Trak Direct Drive XYZ
High Speed for Particle Tracking
- 70x70x50µm XYZ motion
- Direct drive = Higher dynamics
- Complete with digital controller
- Fast response <5msec, subnanometer resolution: ideal for tracking
- Easy integration in microscopes
- Piezoresistive sensors
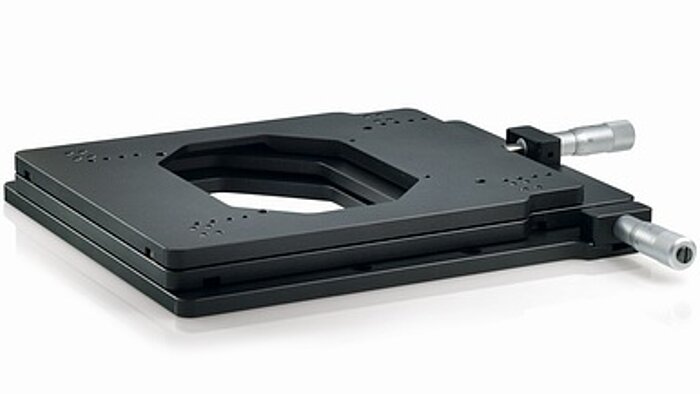
M-545 XY Microscope Stage
High Stability, Manal Micrometers
- 25x25mm travel range
- Highly stable base for P-545 and P-736 PInano® piezo scanning stages
- Low profile for easy integration: 30mm
- Micrometer screws
- For Nikon, Zeiss, Leica and Olympus microscopes
- Motor upgrade available
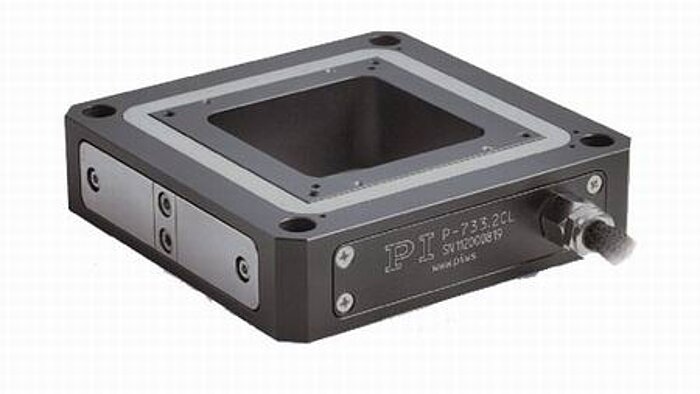
P-733 XYZ Piezo Scanning Stages
Parallel Metrology, 100µm
- 100x100x10µm motion
- <0.3 nanometer resolution
- Capacitive feedback
- 50x50mm aperture
- Frictionless precision flexure guides
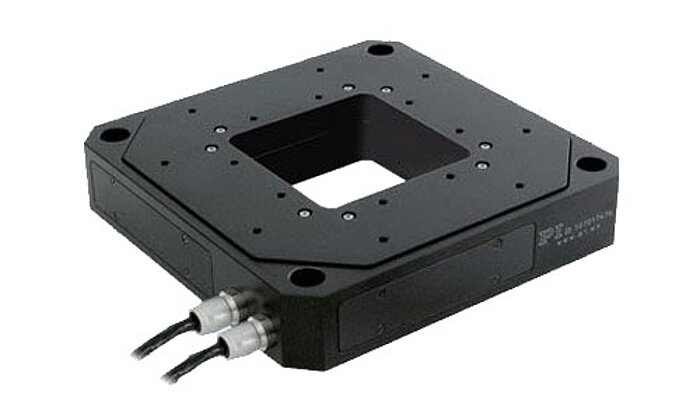
P-561 / 2 / 3 PImars, XYZ Piezo Stage
High End Performance, to 300µm
- 100-300µm XY & XYZ motion
- Six-axis option
- Sub-nanometer resolution
- Ultra-fast XY and XYZ versions
- PICMA® long-life piezo drives
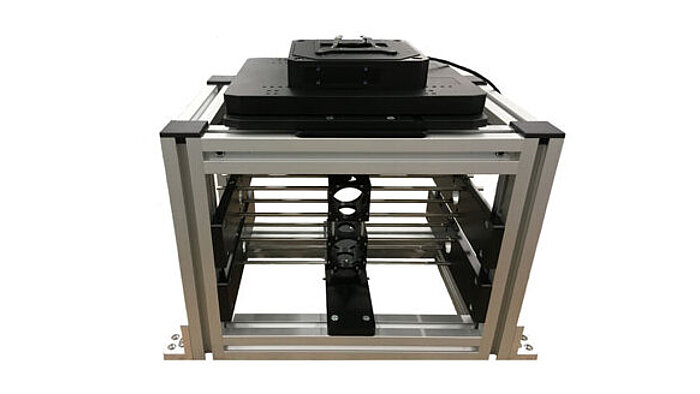
PInano® Stage Platform
Configurable System
- Two horizontal 40mm cage systems
- Four threaded SM1 access ports
- 25x25mm motorized stage
- XY/XYZ nanopositioning stage
- Optional upper breadboard for trans-illumination optics
Single molecule tracking requires very fast motion. Direct-drive piezo stage designs achieve millisecond responsiveness. High powered amplifiers with plenty of short term peak current provide the required bandwidth. The faster the piezo stage, the more important is a highly stable base. Self-clamping ultrasonic motor long-travel positioning stages (such as the PIline U-780) or the M-545 manual stage are essential to take full advantage of the extreme accelerations direct drive piezo scanning stages are capable of.
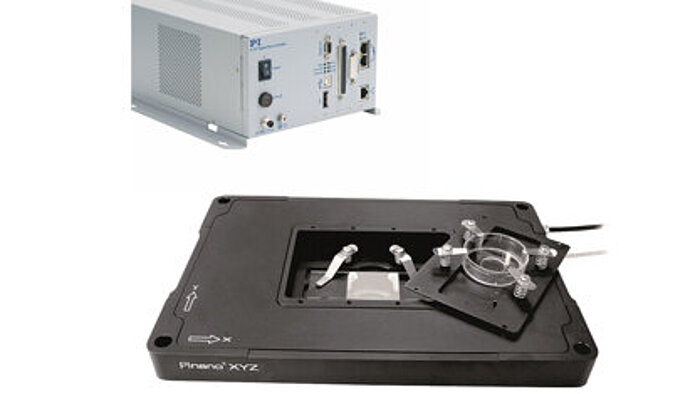
P-545 PInano® Trak Direct Drive XYZ
High Speed for Particle Tracking
- 70x70x50µm XYZ motion
- Direct drive = Higher dynamics
- Complete with digital controller
- Fast response <5msec, subnanometer resolution: ideal for tracking
- Easy integration in microscopes
- Piezoresistive sensors

P-733.3DD High-Dynamics Scanners
Fastest XYZ Piezo Stages
- 30x30x10µm motion
- Direct drive = Higher dynamics
- Up to 2.2 kHz resonant frequency
- 100 picometers resolution
- Frictionless precision flexure guides
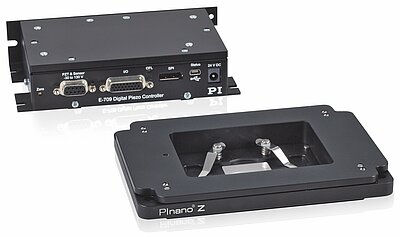
The PInano® P-736 piezo insert Z-scanner is designed as an insert for microscope stages with a 160x110mm standard K-frame opening. It has an aperture of 93x65mm for microscope slides, Petri dishes, etc. A larger version of the P-736 stage with a full size K-frame opening, for well plates etc., is also available.
Digital Control: The PInano® packages include a digital servo controller (not to be confused with an analog servo with USB interface) which provides higher performance (linearity, dynamics) than conventional analog piezo controllers and allows changes to be made on the fly. In addition to USB and Ethernet interfaces, an analog 0-10V interface is also installed – convenient to use with many existing instruments providing analog outputs.
Piezo Resistive Sensors (PRS): Based on high resolution semiconductor strain gauges, often used in AFM’s, they provide a very high signal to noise ratio and low noise.
Capacitive Sensors: Non-contact, direct-metrology sensors that measure the gap of a moving platform against the static frame and provide the highest linearity and very low noise.
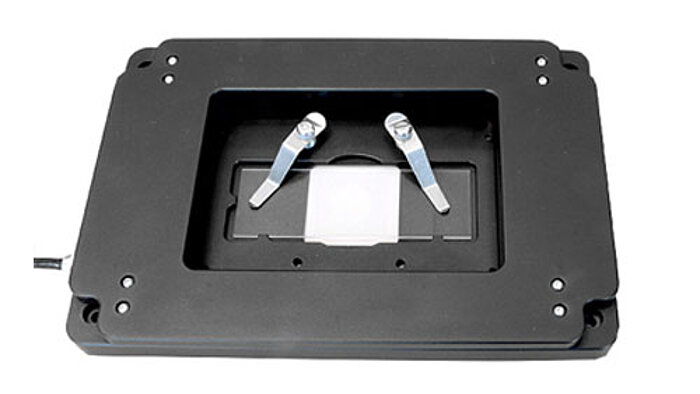
P-736 Piezo-Z Scanner, w/Controller
For Microscope Slides
- 200µm vertical motion
- 1nm resolution
- Fast step & settle, from 5msec
- Low profile: 20mm (0.8")
- Controller & software included
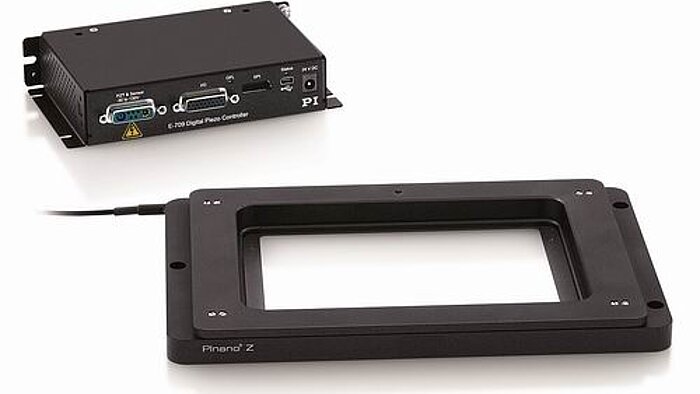
P-736 Piezo-Z Scanner, w/Controller
For Multi Well-Plates
- 220µm vertical motion
- 1nm resolution
- Fast step & settle, from 5msec
- Low profile: 20mm (0.8")
- Controller & software included
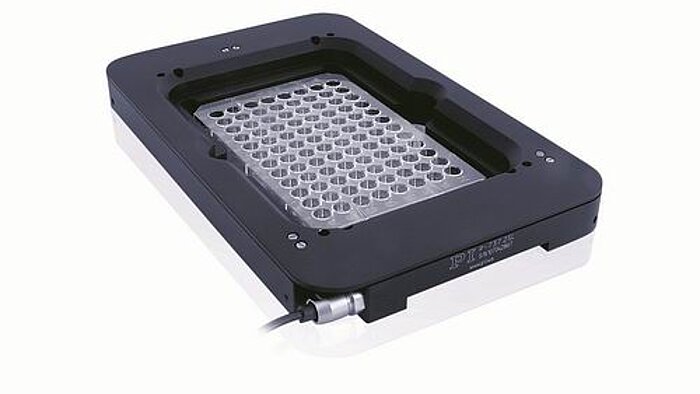
P-737 Piezo Z-Stage
For Microscopy & Biotech
- 100, 250, 500µm motion
- 2-5 nanometer resolution
- Millisecond response
- Aperture for specimen holders
- Integrates with motorized XY stages
Ultra High Stability with Ultrasonic Ceramic Direct-drive Motors
Ultrasonic motors are self-clamping at the end of every move and on power off. This contributes to their extreme position stability (long term drift is significantly improved by the elimination of lubricant flow of screw-drive stages, see article here).
Fast Step & Settle and Wide Dynamic Range
Due to the direct drive and very low inertia, ultrasonic motors provide very fast start/stop behavior in the millsecond range, smooth motion with a very wide dynamic range from microns/second to 100’s of millimeters/second.
How Ultrasonic Motors Work
Both linear and rotary ultrasonic motors are based on compact piezo ceramic elements driven at high frequencies of 10’s to 100’s of kHz (beyond the human hearing range). Each oscillation cycle transfers nanoscopic motion to a linear or rotary ceramic surface bonded to a linear runner or rotary platform.
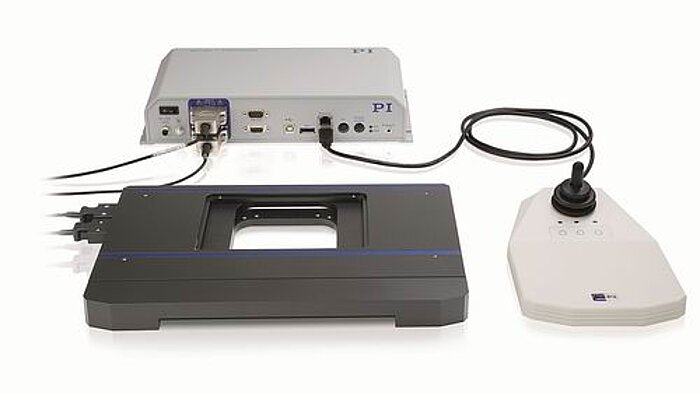
U-760 / U-781 XY Inverted Microscope Stage
Silent Ultrasonic Linear Motor
- 25x25mm & 128x86mm XY motion range
- 10nm encoder resolution
- Up to 120mm/sec velocity
- Combines with piezo flexure scanners
- Self clamping = Ultra-high stability
- With joystick and controller
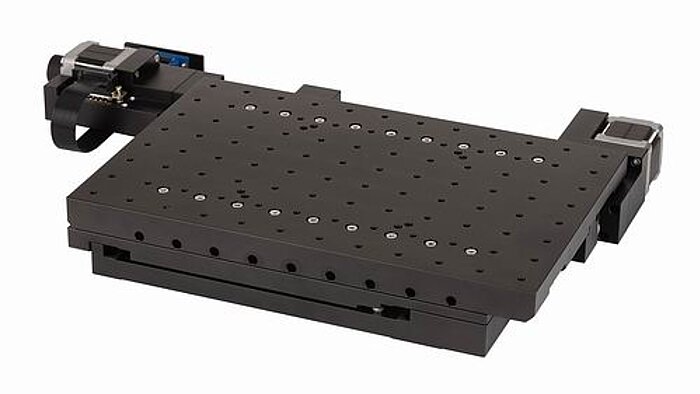
M-971 Motorized XY-Stage for OEMs
Low Cost Stage for Customizations
- 2”x1” XY travel (50x25mm)
- 0.2µm min. inc. motion
- 2.5nm motor resolution
- 10mm/sec max. velocity
- 20kg load
- Stepper motor driven
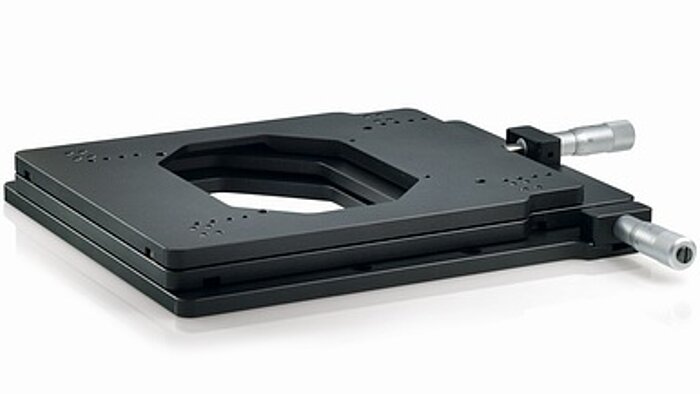
M-545 XY Microscope Stage
High Stability, Manal Micrometers
- 25x25mm travel range
- Highly stable base for P-545 and P-736 PInano® piezo scanning stages
- Low profile for easy integration: 30mm
- Micrometer screws
- For Nikon, Zeiss, Leica and Olympus microscopes
- Motor upgrade available
The U-780 XY linear microscope stage is a novel, low-profile, motorized precision positioning stage for high-resolution microscopes. It comes complete with a controller and joystick. The XY stage is based on PI’s patented ultrasonic ceramic linear motors. This drive technology provides extremely high stability – important for high resolution imaging. The motors are preloaded and automatically clamp when a position has been reached. Compared to conventional screw drives, position drift is significantly reduced. There is also no servo jitter as can be observed with electro-magnetic linear motors. No electric current is required and no heat is generated when resting at a position – further reducing drift and disturbances for highly sensitive measurements. The ultrasonic linear motors provide a very wide dynamic speed range from microns/second and below, up to more than 100mm/sec. A linear encoder with 100nm resolution is integrated for each axis – this direct position measurement principle eliminates play and backlash. The U-780 XY microscope stage systems come with many software tools, such as PIMikroMove, PI General Command Set (GCS), and drivers for LabVIEW. Compatible with µManager, MetaMorph, Andor iQ, MATLAB.
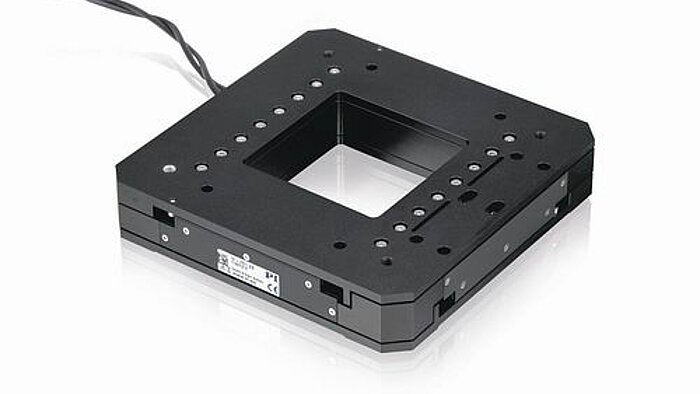
U-751 XY Linear Stage
Silent Ultrasonic Linear Motor
- 25x25mm XY motion range
- 100nm encoder resolution
- 100mm/sec velocity
- 170x170mm footprint
- Self clamping motor design
- Vacuum options
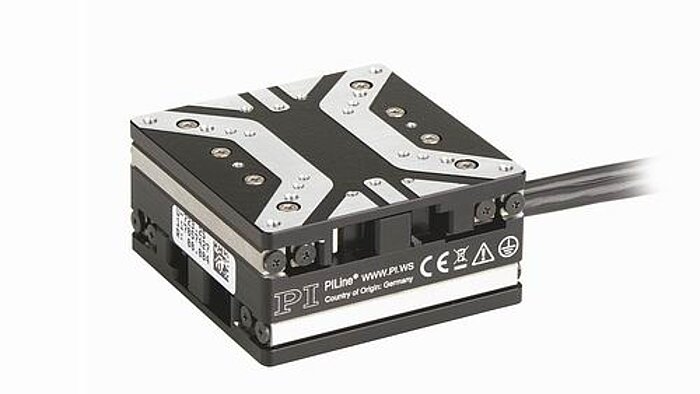
U-723 Miniature XY Linear Stage
Silent Ultrasonic Linear Motor
- 22x22mm XY motion range
- 10nm encoder resolution
- 200mm/sec velocity
- 42x42mm footprint
- Self clamping motor design
- Vacuum options
Miniature Piezo Positioning Stages and Miniature Piezo Motor Actuators
For Innovative Microscopy Applications
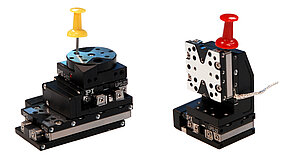
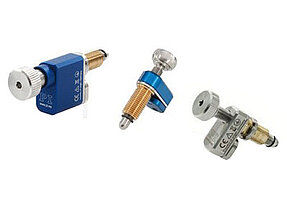
Stick-slip piezo motors (inertia motors) permit the design of the smallest class of precision motorized positioners. The direct drive motors are only a few millimeters in size, there are no gears, or other conventional power transmission components involved that add size, complexity, play or backlash.
Piezo inertia motors make use of the difference in the static and dynamic friction coefficients between two surfaces; their controllers provide a quasi sawtooth output voltage, with a slow expansion phase and a fast contraction phase. In the expansion phase, the piezo actuator moves the slider; in the contraction phase, its inertia prevents the slider from following the quick motion of the actuator, and it remains at its position.
Overview Miniature Piezo Motor Stages
Overview Miniature Piezo Motor Actuators
Hexapod 6-axis parallel positioners are often referred to as Stewart Platforms. A hexapod is based on a 6-axis (XYZ, pitch, roll, yaw) actuator system arranged in parallel between a top and bottom platform. PI's parallel kinematics (PKM) precision positioning systems have many advantages over conventional serial kinematics stages, including lower inertia, improved dynamics, smaller package size, and higher stiffness. In addition, hexapods are more flexible than conventional 6 axis positioners.
Hexapod Articles in Medical Applications
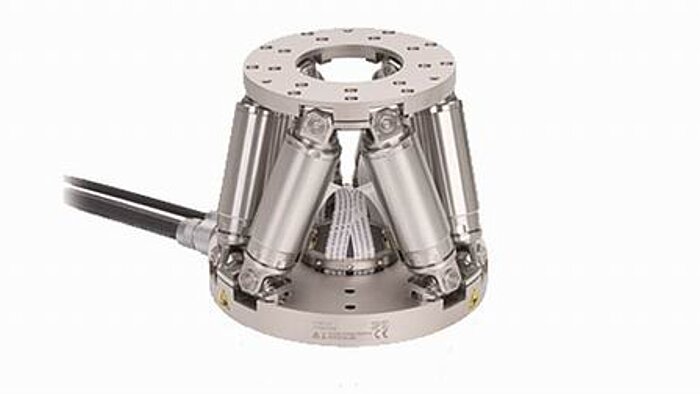
H-811 Miniature Hexapod
Brushless DC Motors
- 34x32x13mm XYZ travel
- 20x20x41° rotary travel
- 5kg load
- 5nm actuator resolution
- 20mm/sec max. velocity
- Ø136mm base, 114mm height
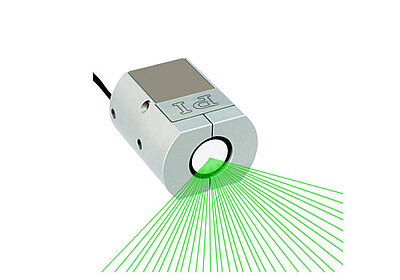
PI's ultra fast piezo steering mirror platforms are based on frictionless flexure guides and high-speed solid-state piezoelectric drives.
Fast and Compact
These compact devices can provide integrated pitch and roll motion with a single moving mirror. They are faster than galvo-scanners and voice-coil driven beam steering systems (also available from PI) and can be used in both static and highly dynamic operation (e.g. scanning, tracking, drift and vibration cancellation).
Advantages of PI Piezo Steering Mirrors
Coplanar multiaxis motion (based on parallel kinematics design), fast response (sub-millisecond), high resolution (up to nanoradian range), long travel ranges (up to 3 degrees optical deflection)
PI's parallel-kinematics multi-axis steering mirrors use only one platform/mirror for all axes. There is one common pivot point and no polarization rotation, an important feature for many precision optics applications.
Overview Piezo Steering Mirrors
PZT tube scanners are often used in scanning microscopy applications. PZT tubes make use of the d31 piezo effect. When voltage is applied, the tube shrinks radially and axially, proportional with the voltage. By segmenting the tube axially, multi-axis motion is feasible and scanning is possible.
PICA Shear actuators can also be used in lateral scanning applications. They are more robust than scanner tubes and come in single axis to XYZ configurations.
P-363 XYZ PicoCube nanopositioning stages are based on shear actuators and capacitive position feedback sensors.
The P-313 XYZ scanner is made of a highly linear crystalline electroactive material and does not require position feedback sensors and closed-loop operation. The advantage is extremely high bandwidth and picometer precision, but at small travel ranges of 1µm.
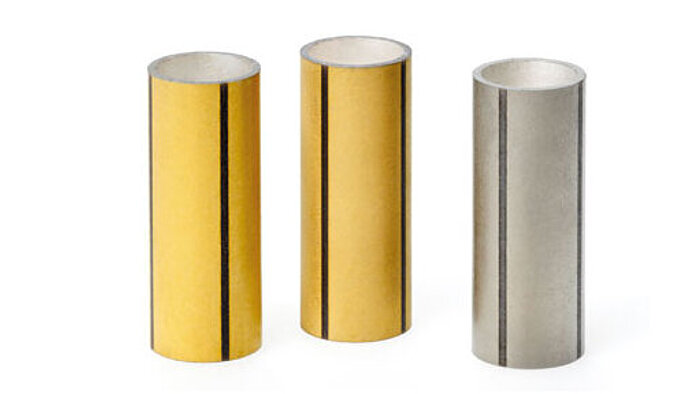
PT230 Piezo Scanner Tube
Radial and Axial Motion - Fast
- 70mm max. length
- 2 to 80mm OD
- 0.8 to 74mm ID
- 0.30mm min. wall thickness
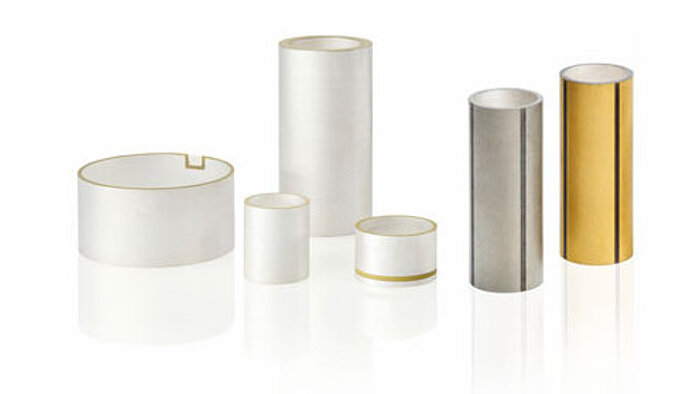
PT120 – PT140 Piezo Tubes, Scanners
From <2mm Diameter
- Miniature size option
- XYZ-scanner option
- Wall thickness as small as 0.3mm
- Sub-nanometer resolution
- Large diameters to 80mm
- Based on d-31 piezo effect
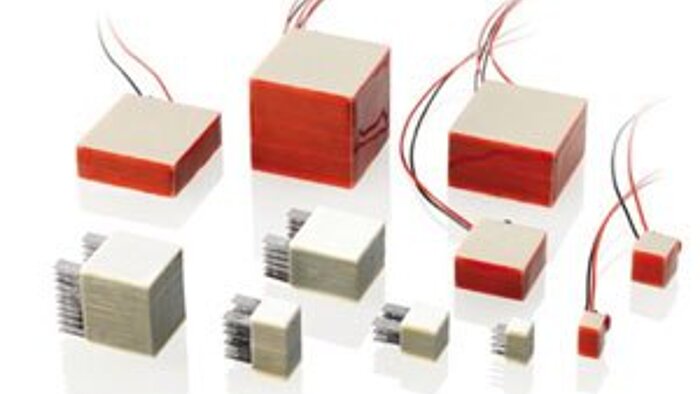
P-111 – P-151 Piezo Shear Actuators
Compact Multi-Axis Positioners
- X, XY, XZ and XYZ versions
- To 10µm travel
- For fast scanning
- Options: clear aperture, UHV
- Extreme reliability >1B cycles
- Picometer-resolution / Sub-msec response