Active Photonics Alignment Systems / Fiber Optic Alignment Stages can save 99% Alignment Time
Algorithms, Motorized Fiber Positioners, and Automated Sub-Systems for Silicon Photonics and Optics Alignment
PI provides the world’s fastest photonics alignment engines, designed to significantly improve array alignment times, silicon photonics production economics and reduce costs in high-volume PIC testing. Our solutions span from innovative single and dual-sided 6-DOF active fiber optic alignment engines to economical motorized fiber positioners. PI’s state-of-the-art hexapod and air-bearing alignment engines have excelled in high-throughput, silicon-photonics wafer probing and packaging automation, as well as in applications related to optical lens assembly, telecommunications, and data communications.
Advanced Array Alignment
All our automated alignment systems benefit from PI’s leading-edge search and alignment algorithms that are running embedded on our high-performance alignment controllers. Users have a choice of hexapod-based mechanics, modular, air bearing-based solutions, and economical stepper motor-based stages, all designed for industrial photonics automation. All systems come with extensive software for easy setup and integration. Ultra-fast piezoelectric scanning & alignment modules are also available as stand-alone systems. Our F-712, 6-DOF systems enable fast, parallel alignment of array components. The intelligent parallel gradient search algorithm can optimally align and track all I/Os in array devices simultaneously, ensuring lowest loss, highest production throughput and best yield.
In addition to solutions for fiber-optics-based photonics applications, PI offers fast laser beam steering systems for free-space-optical communication, also compatible with our ultra-fast search and lock-on algorithms.
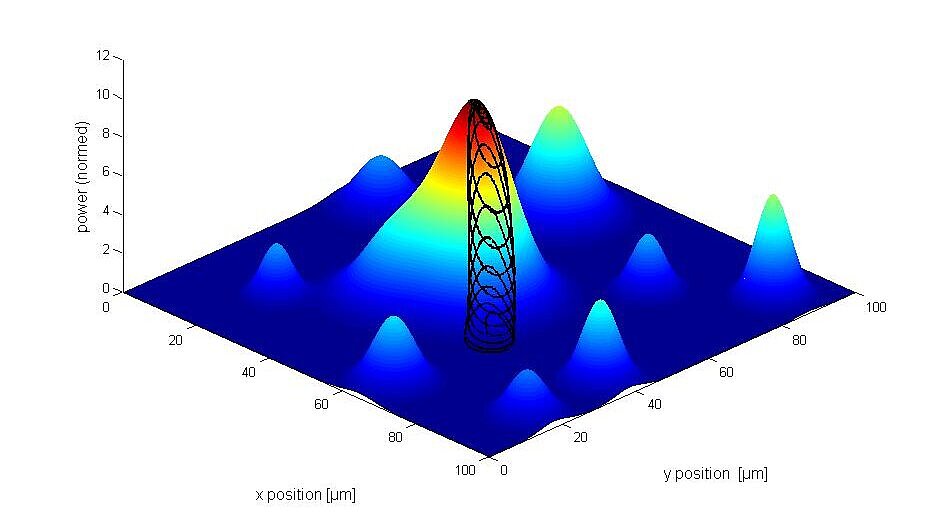
PI’s alignment systems and ultra-fast array alignment algorithms were developed to significantly improve production economics in photonics test and assembly applications. In addition to our award-winning FMPA (Fast Multichannel Photonics Alignment) algorithms that can reduce multi-axis aligment time by 99%, our team has now also solved the first-light capture problem with a new algorithm called PILightning. This new technology promises to reduce first-light capture time by orders of magnitude and is outpacing any other technique currently used for automated photonics alignment. In dual-sided first-light capture tests, we have seen improvements of 500X and more.
PI’s active alignment algorithms can scan a device quickly for characterization purposes, optimize power with a fast gradient search routine and optionally track them to mitigate drift processes and disturbances. Our technology reduces alignment time by orders of magnitude while achieving ultralow-loss alignment performance, with arrays exhibiting a typical coupling repeatability of 0.02dB.
PI’s Fast Multi-Channel Photonics Alignment Engines (FMPA) are based on a highly specialized digital motion controller (E-712) and a hybrid active alignment mechanism to achieve the required long travel ranges without sacrificing stability, resolution or alignment speed.
Silicon Photonics (SiP) means photonic devices are now being fabricated alongside microelectronics on silicon wafers. Testing and packaging these requires nanoscale alignments across multiple channels with high throughput. Testing (especially at the wafer level) and packaging economics both demand extraordinary speed and parallelism. SiP is a mission-critical, industry-wide initiative across the semiconductor field, and also the animating energy behind photonics’ resurgence. PI’s FMPA is the fastest, most flexible, most robust solution.
FMPA is implemented in the E-712 controller’s modular firmware to enable fast, simultaneous alignment and tracking of multichannel couplings in multiple degrees of freedom. A broad variety of coarse/fine mechanisms can be used, enabling a spectrum of applications from undiced wafer to final package. Long-travel, closed-loop piezo nanopositioners ensure high throughput and reliable reproducibility. High-precision stage stack or hexapod options accommodate any application up to 6 DOFs per coupling.
Alignment options include a new multidimensional gradient search for aligning and tracking any number of input and output couplings even if they interact. Scanning and modeling functionalities identify global maxima and accurately determine the centroid of quasi-Gaussian, tilted Gaussian, top-hat and tilted top-hat couplings at high speed. Typical alignment modalities complete within a few hundred milliseconds, and time for gradient search alignment and tracking is virtually independent of the number of couplings and degrees-of-freedom. The F-712 high-speed optical power meter is recommended for high-throughput applications.
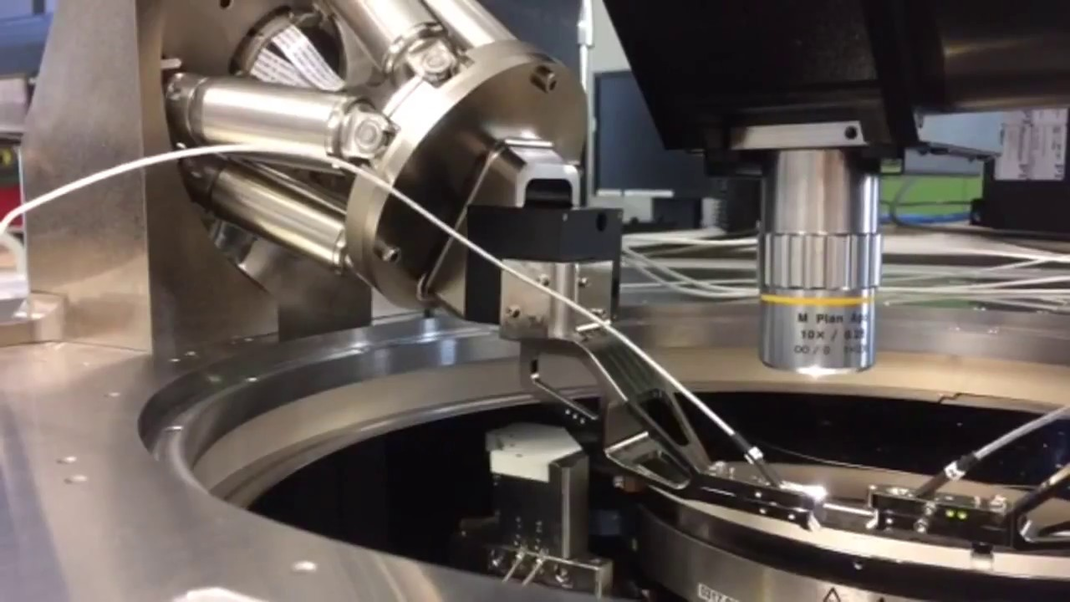
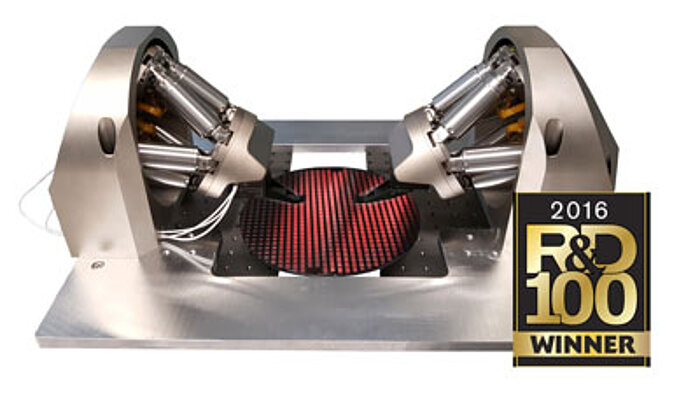
F-712 6-Axis Fast Photonics Alignment System (FMPA)
Single & Double-Sided, Upright & Low-Profile, Fully Automated
- Ideal for array alignment
- Ultra-fast automatic alignment <0.5s
- Hybrid design – Motorized stages for long travel, piezo flexure scanners for fast and wear-free motion
- Complete with mechanics, controllers, and software
- Integrated scan & alignment routines
- Closed-loop position control for high accuracy and operational reliability
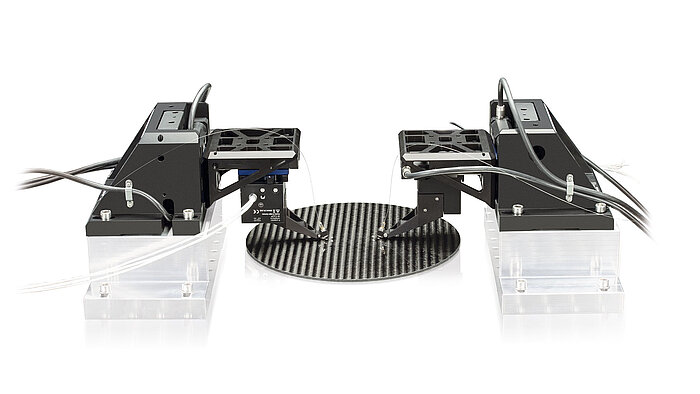
Fast Photonics Alignment System (FMPA)
Single/Double Sided Automated XYZ Photonics Alignment
- Ultra-fast automatic alignment <0.5s
- Hybrid design – Motorized stages for long travel, piezo flexure scanners for fast and wear-free motion
- Complete with mechanics, controllers, and software
- Integrated scan & alignment routines
- Closed-loop position control for high accuracy and operational reliability
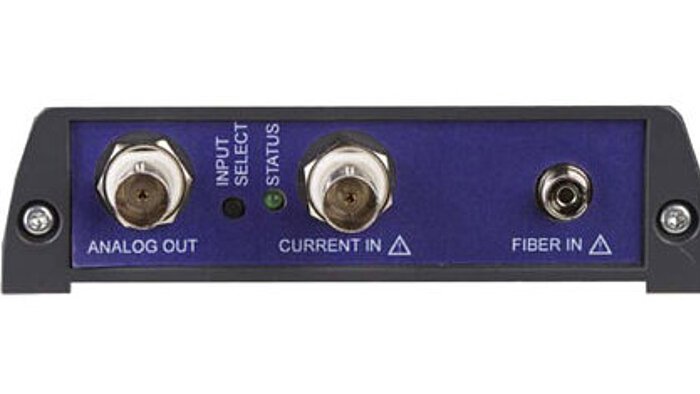
F-712.PM1 High Speed, High Bandwidth Optical Power Meter
- 20kHz signal bandwidth
- 85nW to 85mW dynamic range
- 400 -1550nm wavelength
- 0 - 1mA input current
- Logarithmic output
PI‘s hexapod-based photonics alignment systems provide 6 degrees of freedom motion with nanometer range resolution. The hexapod controller has many built in routines for commands finding first light and optimizing the alignment. A n optional analog input can be used with optical power meters. The user-programmable pivot point is a significan advantage – it can be set to any location, for example the tip of a fiber, the waist of a beam or the surface of an SiP wafer. The F-712 high-speed optical power meter is recommended for high-throughput applications.
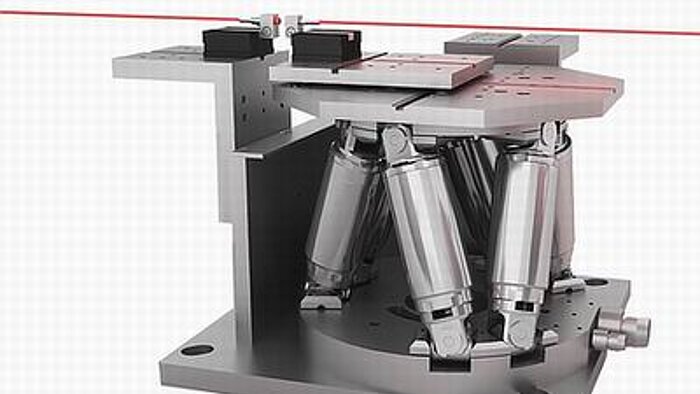
H-811 Automated Miniature 6-Axis Photonics Alignment System
Very Compact Stewart Platform Design
- Integrated scan and alignment routines for single mode fibers, collimators, arrays, and I/O chips and optics
- Extensive software package
- User-programmable center of rotation (pivot point)
- 5nm actuator resolution
- Travel ranges XYZ: ~34mm; θXYZ up to 42deg
- Velocity to 10mm/sec
- Parallel kinematics with 6 degrees of freedom for reduced mass and faster Settling
- No moving cables, reduced friction, higher reliability
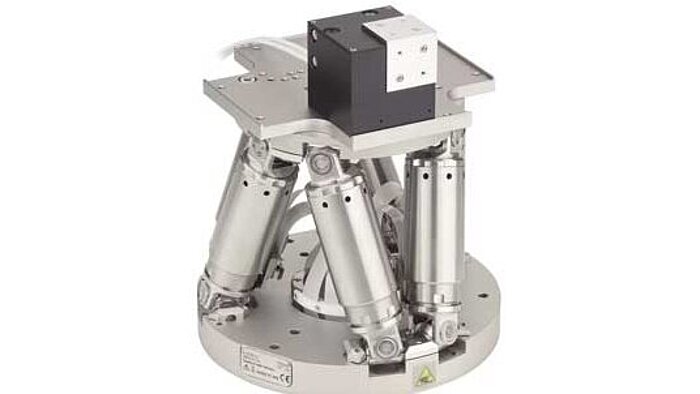
H-811 Automated Miniature 6-Axis Photonics Alignment System
With XYZ Piezo Scanner
- Ideal for array alignment
- Piezo scanner for higher speed & higher resolution
- Integrated scan and alignment routines for single mode fibers, collimators, and I/O chips and optics
- Extensive software package
- User-programmable center of rotation (pivot point)
- 5nm actuator resolution
- Travel ranges XYZ: ~34mm; θXYZ up to 42deg
- Velocity to 10mm/sec
- Parallel kinematics with 6 degrees of freedom for reduced mass and faster Settling
- No moving cables, reduced friction, higher reliability
PI’s modular alignment engines also benefit from our advanced FMPA alignment technology. They are based on a combination of linear stages, and tip/tilt stages or goniometers for rotation. In the case of the F-308, F-408 and F-508 XYZ systems, linear motor stages (frictionless counterbalance on the Z-axis) are used. The F-143, F-142 and F-716 alignment systems employ air bearings and direct drives to completely eliminate friction, wear, and particle generation, ideal for critical 24/7 applications. These systems are also available with PI’s ultra-fast first-light capture algorithm, embedded in the alignment controller firmware.
In the case of the F-131, a Piezo XYZ scanner is mounted on a long travel XYZ motorized stage. The piezo scanner allows for ultra-fast scanning and alignment, or for mapping the output characteristics of an optical device in fractions of a second. The F-712 high-speed optical power meter is recommended for high-throughput applications.
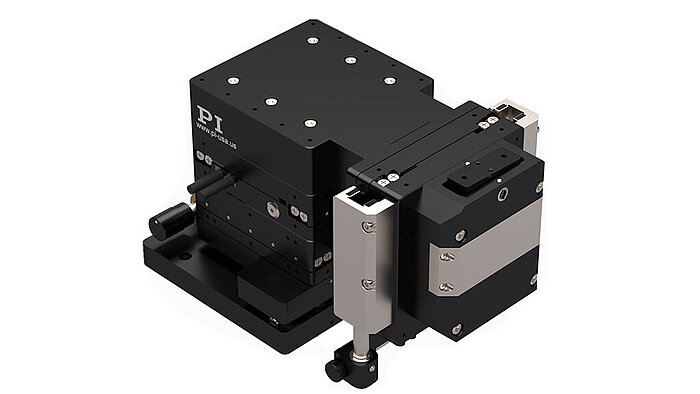
F-141 Compact Direct-Drive, 2DOF to 6 DOF Fast Photonics Alignment System
High Performance Controller and Alignment Algorithms
- Ideal for array alignment
- Cost-optimized modular, 2DOF to 6DOF 3rd generation photonics alignment platform
- Advanced alignment algorithms onboard for out-of-the-box alignment and tracking
- Open-source LabVIEW code and host programming libraries for easy development
- Long-life, non-contact linear motors on all axes enabling higher-throughput and lifetime
- Fast 40x40x40mm XYZ / 12° Theta-Y travel
- Optional manually adjustable Theta-X/Z base, 5° travel
- Integrated non-contact Z counterbalance
- Optional high performance power meter
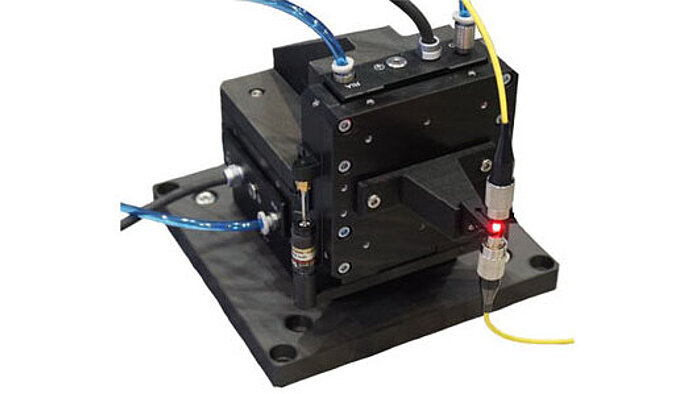
F-142 Air Bearing Multi-Axis Alignment System
High Performance Controller and Alignment Algorithms
- Zero-wear, air bearing-based, ultra-compact, photonics alignment platform
- Controller with embedded high-speed algorithms for out-of-the-box alignment and tracking
- Open-source LabVIEW code and host programming libraries for easy development
- Non-contact linear motors on all axes enabling higher-throughput and lifetime
- 10mm travel, 10nm resolution, XY and XYZ configurations
- Integrated non-contact counterbalance on the vertical axis
- Optional high-performance power meter
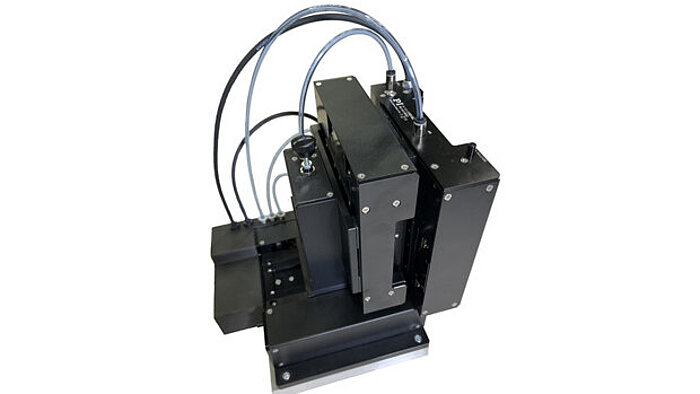
F-143 Air Bearing Multi-Axis Alignment System
High Performance Controller and Alignment Algorithms
- Zero-wear, air bearing-based, compact, photonics alignment platform
- Controller with embedded high-speed algorithms for out-of-the-box alignment and tracking
- Open-source LabVIEW code and host programming libraries for easy development
- Non-contact linear motors on all axes enabling higher-throughput and lifetime
- 25mm travel, 1nm resolution, XY and XYZ configurations
- Integrated brake and non-contact counterbalance on the vertical axis
- Optional high-performance power meter
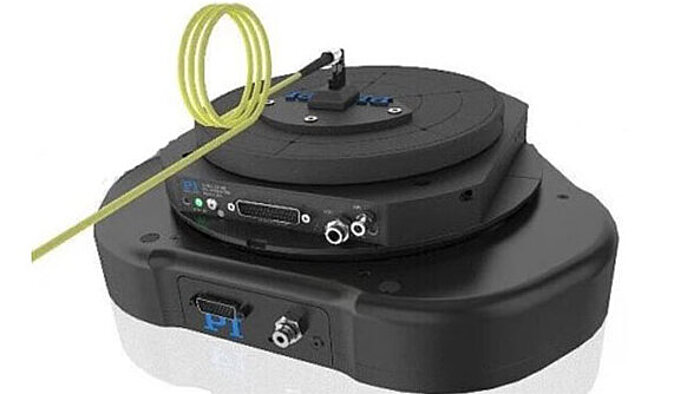
F-716 6-DOF Air Bearing Alignment System
High Performance Controller and Alignment Algorithms
Zero-wear, air bearing-based, 6-axis, direct-drive photonics alignment platform with user programmable pivot point
Advanced Alignment Algorithms onboard for out-of-the-box alignment and tracking
Open source LabVIEW code and host programming libraries for easy development
Long-life, non-contact linear motors on all axes enabling higher-throughput and lifetime
10nm resolution, 5mm XYZ travel, 2° θ- XYZ rotation
Low profile: 100mm
Optional high-performance power meter
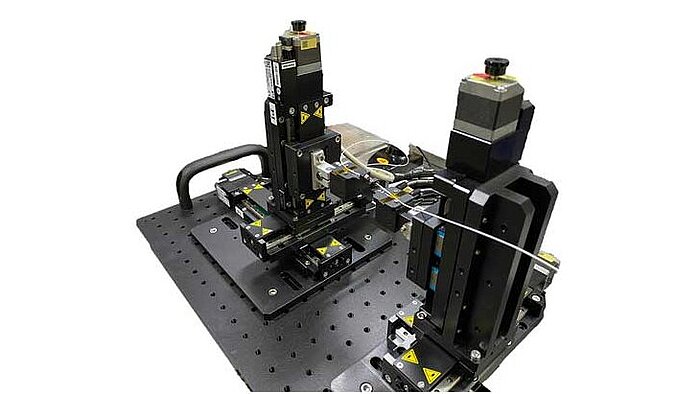
F-836 Economical Fiber Aligner
Modular, with High Performance Controller
- Modular design with travel range to 200mm
- Direct-drive stepper motors, with linear encoder option
- Single and double-sided configurations
- Advanced Alignment Algorithms embedded in controller firmware for out-of-the-box alignment and tracking
- Open-source LabVIEW code and host programming libraries for easy development
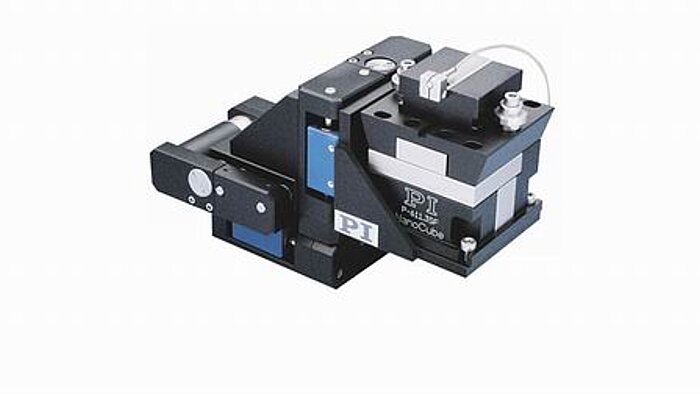
F-131 Compact XYZ Motorized Fiber Alignment System
With Piezoelectric High Speed Photonics Alignment Module
- Unique 2-stage high-speed aligner (fiber positioner)
- Closed-loop position control for high accuracy and operational reliability
- 15mm motorized travel with servo motors with 50 nm resolution
- 1nm resolution, high speed piezo scanning unit 100x100x100µm for ultra-fast complete device characterization
- Complete package with software, C-884.4DC motor controller and E-727.AS piezo controller
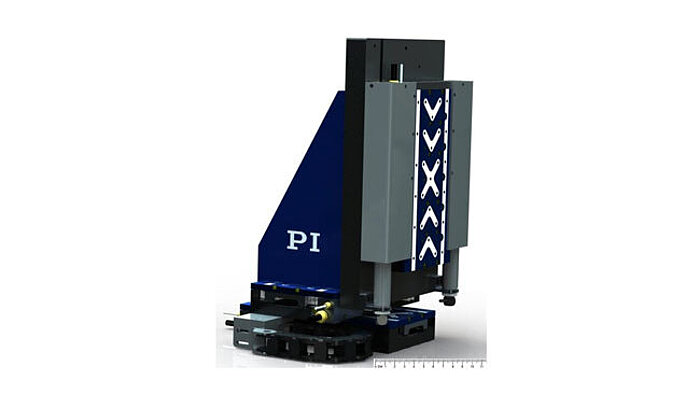
F-508 Direct-Drive, Multi-Axis, Photonics Alignment System
High Performance Controller and Alignment Algorithms
- Compact, modular, 3rd generation photonics alignment platform
- Advanced Alignment Algorithms onboard for out-of-the-box alignment and tracking
- Open Source LabVIEW code and host programming libraries for easy development
- Long-life, non-contact linear motors on all axes enabling higher-throughput and lifetime
- Absolute encoder option for power cycle position repeatability and collision safety
- 0.5nm Resolution, 80x80x80mm travel
- Integrated non-contact Z counterbalance
- Optional high performance power meter
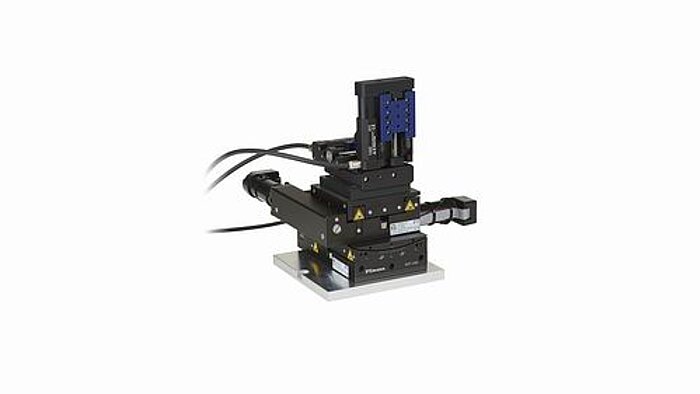
F-122 Compact 5-Axis Motorized Fiber Positioner / Aligner
Precision XYZ Stages and Goniometers
- Closed-loop position control for high accuracy and operational reliability
- 25mm XYZ travel, 10° θX, θY
- 0.1µm linear resolution, 4µrad rotational resolution
- Safety due to integrated sensor technology
- Maximum velocity of 20mm/sec and 15°/sec
These Piezo XYZ scanners are flexure based for elimination of friction, backlash and wear. They provide nanometer resolution and millisecon responsiveness, ideal for ultra-fast scanning and alignment, or for characterisation of the output profile of an optical device in fractions of a second. The E-727 piezo controller and the F-712 high-speed optical power meter is recommended for high-throughput applications.
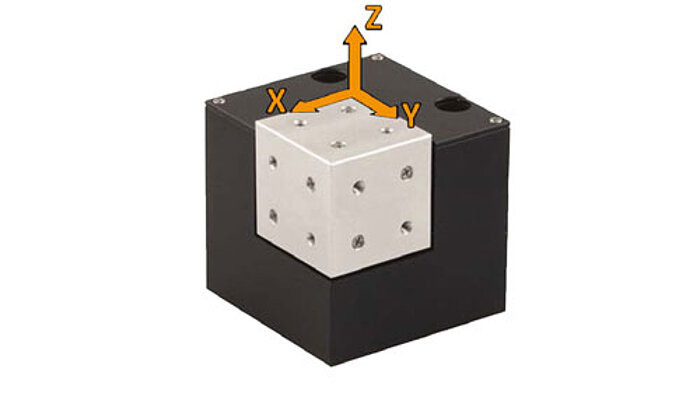
P-616 NanoCube® Compact XYZ Piezo Scanner
Parallel Kinematics Design for Higher Performance
- Closed-loop position control for high accuracy and operational reliability
- Fastest response with minimized inertia from parallel-kinematic design, flexure guided design
- 100µm XYZ travel in compact 40x40x40mm envelope
- <0.2nm resolution/repeatability
- Wear-free and maintenance-free flexure guiding system, solid state drives, and non-contacting sensors
- Ideal for fiber positioning, optic alignment and photonics packaging applications, single mode fiber positioning
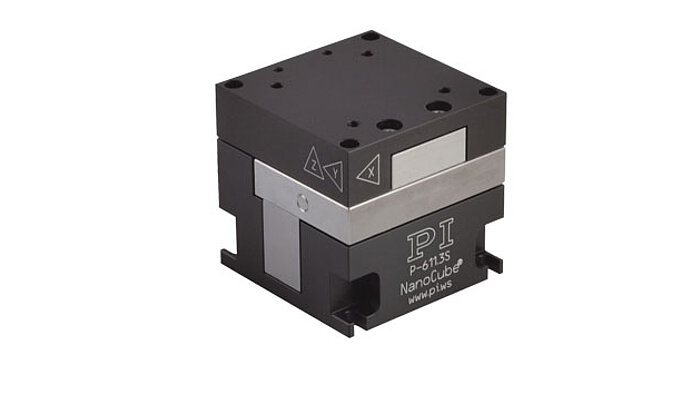
P-611 NanoCube® Compact XYZ Piezo Scanner
Serial Kinematics Design for Lower Cost
- Closed-loop position control for high accuracy and operational reliability
- Lower cost, higher load compared to P-616
- 100µm XYZ travel
- 1nm resolution/repeatability
- Wear-free and maintenance-free flexure guiding system, solid state drivess and non-contacting sensors
- Ideal for fiber positioning, optic alignment and photonics packaging applications, single mode fiber positioning
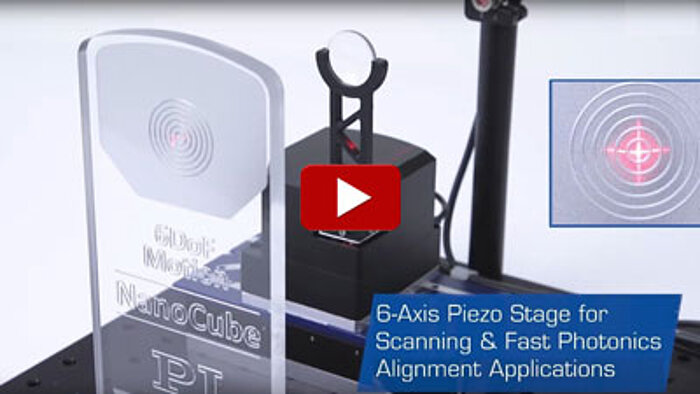
6-Axis Nanopositioning and Fiber Alignment Applications
Watch Video
PI's NanoCube® 6-axis piezo stage device delivers high dynamics with high guiding accuracy.
Piezo tip/tilt platforms provide kHz-range bandwidth with nano-radian resolution, ideal prerequisites for fast and precise beam steering applications such as required for free space optical communication (FSOC). FSOC technology can be used to transmit high data-rates based on light propagation without the use of fibers or waveguides, similar to radio wave-based telecommunication. Based on laser light, the beam is extremely focused and needs to be directed to a receiver very precisely, which requires a mechanism to actively steer it to compensate for deviations caused by environmental influences.
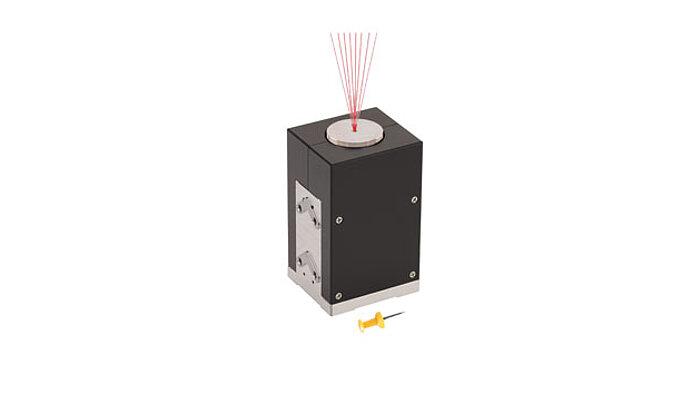
S-335 Compact Piezo Tip/Tilt Platform for Free-Space Optical Telecommunication
High-Speed/Long Travel Piezo Flexure Design
- Optical beam deflection to 70mrad (4°)
- For mirrors up to 25.4mm (1") diameter
- Frictionless, maintenance-free high-precision flexure guiding system
- Parallel kinematics for enhanced dynamics and better multi-axis accuracy
- Factory installed mirror optional
- Mars-Rover tested long-life piezo actuators
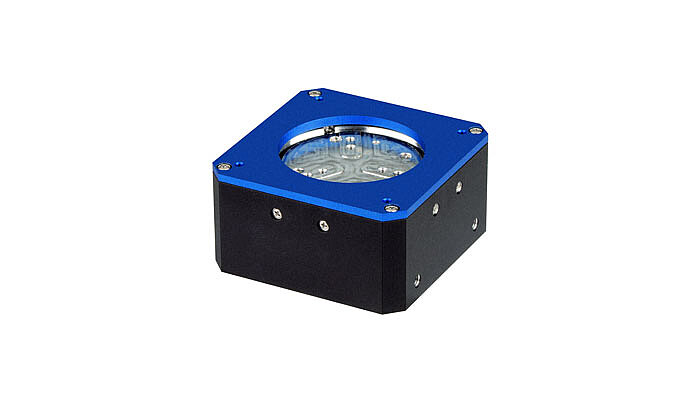
V-931 Fast Steering Mirror Platform
Voice-Coil Driven, Mirrors to 1”
- 140mrad (8°) optical deflection
- <1 µrad resolution
- Closed-loop voice coil drives
- PKM = Equal dynamics for both axes
- 20msec step response