Piezoelectric Actuators, Piezo Transducers: Piezo Stacks, Flexures, Tubes, Benders, Shear Actuators...
Piezoelectric actuators (transducers) are precision ceramic actuators which convert electrical energy directly into linear motion with high speed, force and virtually unlimited resolution. These actuators are used in every modern high tech field from semiconductor test & inspection to super-resolution microscopy, bio-nanotechnology and astronomy/aerospace technology. Read article on reliability in industrial / space applications.
Different Types of Piezo Acutators/Motors: PI provides many different types of piezo actuators and motors: from stack actuators to flexure guided, motion amplified assemblies; from stick-slip mini motor stages to high speed ultrasonic motors for linear and rotary motion. But also tubes, benders, shear actuators and flexible transducers, are available.
Encased Stack Actuators, Multilayer and Discrete, Water Proof Actuators, Preloaded – Motion to 180µm, Force to 30kN
It is important to understand the principles to pick the best type for an application. For more information on the differences between piezo motors and actuators and their applications watch the video below, refer to the piezo motion tutorial or just contact a PI applications engineer for help.
High Curie / Operating Temperatures: PI's piezo ceramic formulation boasts a high Curie temperature for a wide operating temperature range. PI's discrete actuators and the PICMA cofired stacks are available for operating temperatures up to 200 deg C.
PI's award-winning and MARS-Rover-Proven PICMA® ceramic-encapsulated co-fired piezo stacks are polymer-free and combine superior performance with extremely long lifetime. PI's piezo ceramic design and manufacturing division - PI Ceramic - provides the capability and flexibility to offer highly engineered custom sub-assemblies at a very attractive price.
100 Billion Cycles of Life Testing, Space Qualified
PICMA® actuators are space qualified and were submittet 100 billion cycles of life testingat NASA's JPL. Additional piezo life testing results are available for download here.
Custom & Value Added Assemblies / Manufacturing
Information on Value Added Piezo Assemblies from PI Ceramic
Introduction to Flexure-Guided and Motion-Amplified Piezo Actuators
Flexure-guided and motion-amplified piezo ceramic actuators provide longer displacement ranges compared to piezo stacks in a more compact package. They are designed with protective preloads and several types of integrated flexure-guiding mechanisms are feasible depending on the guiding precision required in the application.
PI provides a large variety of standard and custom designs.
- Travel ranges to 1mm and more feasible
- Fast response, Sub-millisecond feasible
- Extreme reliability: Tests at NASA's JPL have shown 100 billion cycles of life
- Sub-nanometer resolution
- Vacuum-compatible versions
- Closed-loop versions
- Backlash-free construction
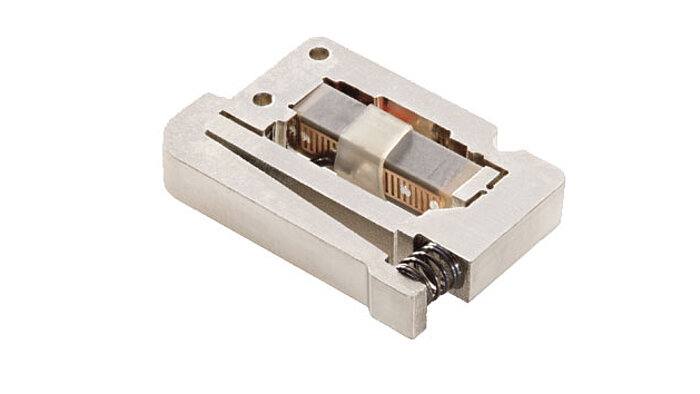
P-604 Low-Cost, Piezo Flexure Actuator
300µm Motion, Flexure Guided
- 300µm travel
- Cost-optimized for large quantities
- Lightweight construction, only 4 grams
- Flexure guided = Frictionless & straight motion
- Small footprint of 13x20mm
- PICMA® long-life piezo actuator
- For OEM instrumentation
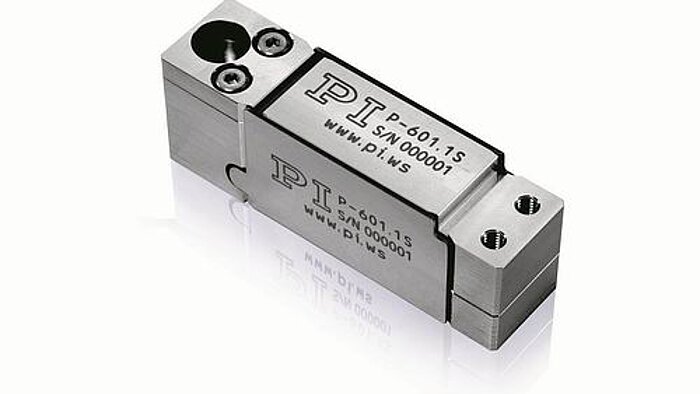
P-601 Piezo Flexure Actuator
Closed-Loop Option
- 100, 250 and 400µm travel
- Position sensor option for closed-loop operation
- Flexure guided = Frictionless & straight motion
- High dynamics and stiffness
- PICMA® long-life piezo actuator
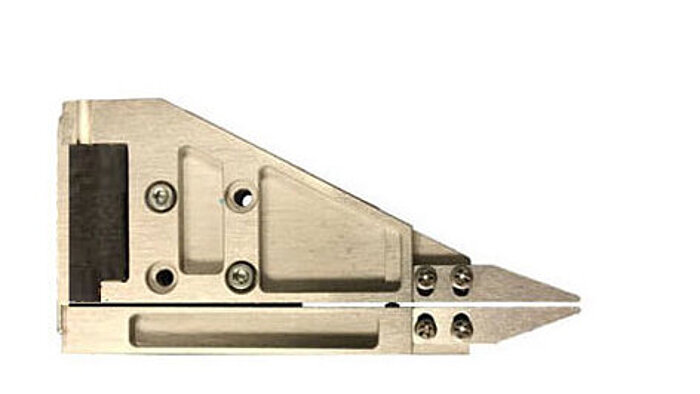
P-900 Piezo Actuated Gripper
Force Control with High Sensitivity
- Closed Loop Force Control at the Gripper Jaws
- Blocking Force = 4N
- Unloaded Travel = 500µm
- Force sensitivity = 0.01N
- Response time = 10msec
- Mass <20g
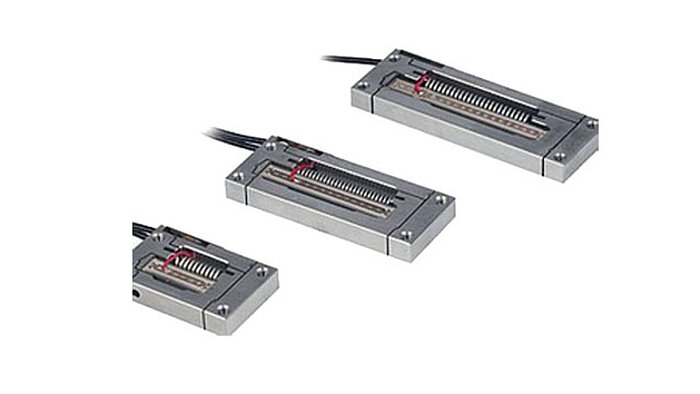
P-603 Piezo Flexure Actuator
Motion to 500µm
- 100, 300 and 500µm travel
- Position sensor option for closed-loop operation
- Compact, cost-effective design
- Flexure guided = Frictionless & straight motion
- High dynamics and stiffness
- PICMA® long-life piezo actuator
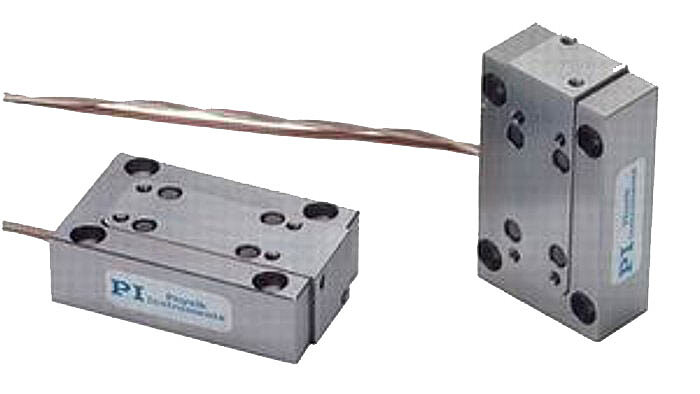
P-753 Piezo Flexure Stage/Actuator
Direct Drive, Highest Dynamics
- 38µm travel
- 0.05nm resolution
- Capacitive feedback = Highest precision
- Direct drive = Ultra-fast response
- Frictionless precision flexure guides
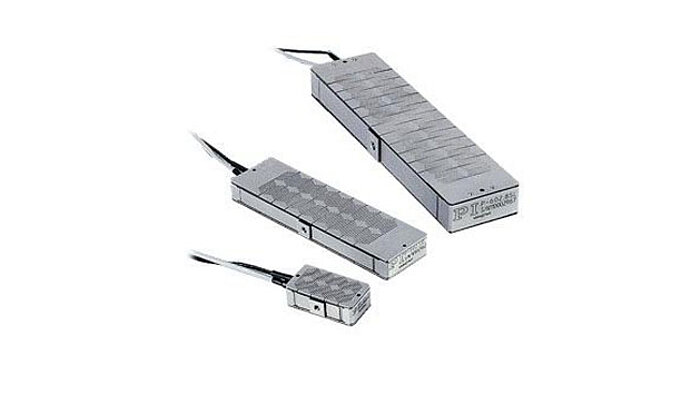
P-602 Piezo Flexure Actuator
Motion to 1mm, High Force
- Up to 1mm travel
- Position sensor option for closed-loop operation
- Flexure guided = Frictionless & straight motion
- To 400N force, high stiffness & dynamics
- PICMA® long-life piezo actuator
These flexure actuators are driven by PI’s ultra-reliable cofired PICMA® piezo stacks. PICMA® actuators have been tested by NASA/JPL running 100 billion cycles with no failures.
Custom flexure actuator designs with larger travel ranges, higher forces or faster response, as well as non-magnetic versions are feasible.
Applications: Flexure actuators are ideal for OEM applications in biotechnology, nano-dispensing, microfluidics, valve control, fast switching and nanopositioning, optics, medical-devices, life-sciences.
These encased piezoelectric actuators are drivenby cofired multilayer PICMA® piezo stacks. PICMA® piezo stacks are extremely reliable and survived 100 billion cycles of life-testing and harsh environments in space and on the Mars Rover with no failures.
Preloading a piezo stack inside a case by means of special springs allows the actuator to handle higher tensile forces.
Hermetically sealed actuators with inert gas filling can be used in harsh environments.
Custom actuator designs with larger travel ranges, higher forces or faster response, as well as non-magnetic versions are feasible.
Applications: Piezo actuators can provide high forces and virtually unlimited positional resolution down to the sub-nanometer range. They make for ideal “OEM motion engines” in fields such as biotechnology, nano-dispensing, microfluidics, fast switching and valve control, nanopositioning, optical alignment, microscopy, medical-devices, and life-sciences.
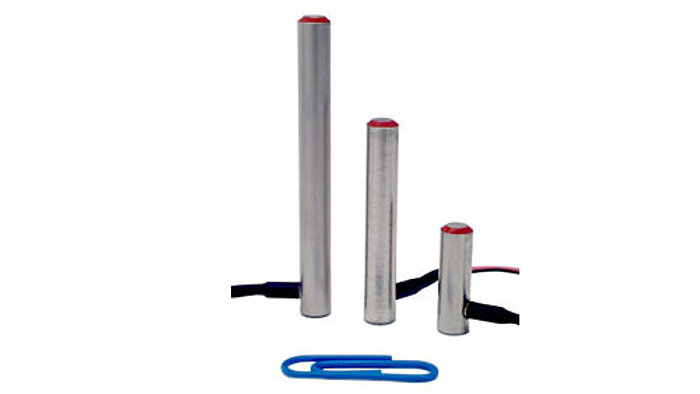
P-810/30 Piezo Stack Actuators
Encased, Small Loads
- 15µm to 60µm displacement
- Pushing forces to 1000N
- Pulling forces to 5N
- Sub-ms response
- Sub-nanometer resolution
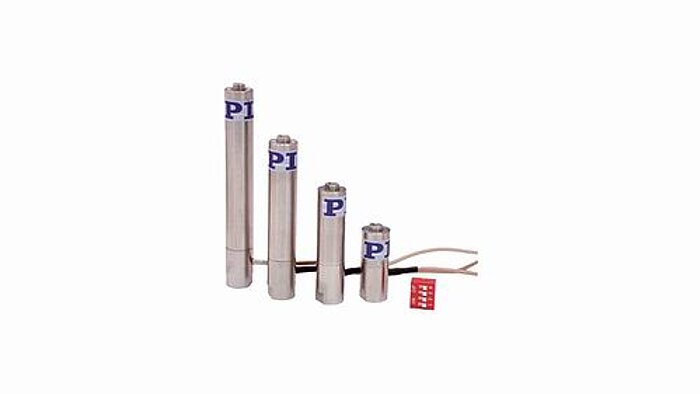
P-840, P-841 Preloaded Piezo Stack Actuators
1000N Load, Closed-Loop Option
- 15 to 90µm displacement
- Pushing forces to 1000N
- Preloaded for pulling forces to 50N
- Closed-loop for high accuracy
- Sub-millisecond response
- Sub-nanometer resolution
- Options: ball tip, vacuum versions
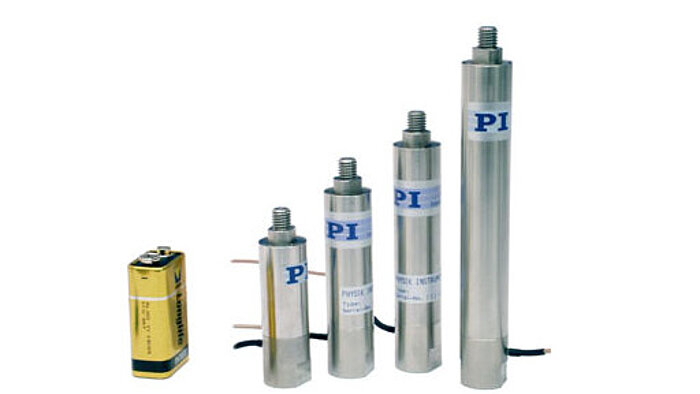
P-844/45 Preloaded Piezo Stack Actuators
3000N Load, Closed-Loop Option
- 15 to 90µm displacement
- Pushing forces to 3000N
- Preloaded for pulling forces to 700N
- Closed-loop for high accuracy
- Sub-millisecond response
- Sub-nanometer resolution
- Options: ball tip, vacuum versions
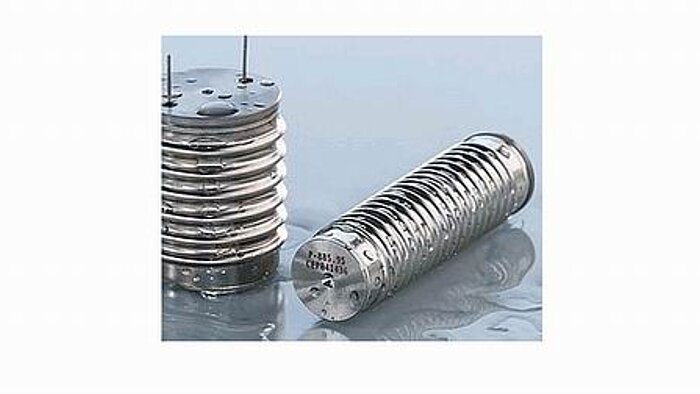
P-88x Waterproof Piezo Actuator
For Harsh Environments
- Waterproof and oil-proof
- Cofired monolithic piezo stacks
- Hermetically sealed steel container
- Inert gas filling
- Optional heat conducting compound filling
- Superior lifetime
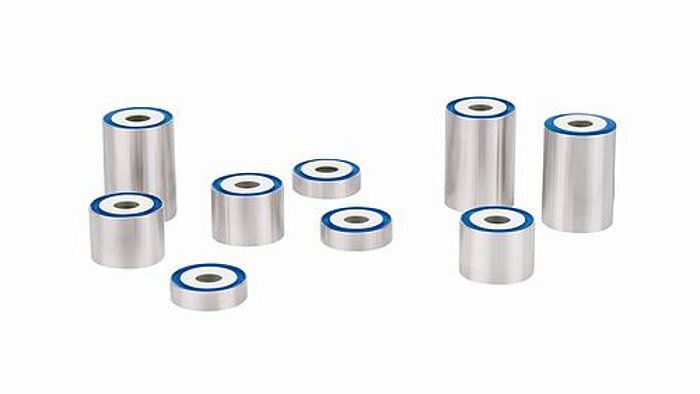
P-131 Programmable Piezo Shims
Set, Forget, Reprogram
- Easy readjustment of machines / optics in inaccessible locations
- Load capacity up to 4000 N per piezo shim actuator
- Long-term stable without permanent power supply
- Avoids time-consuming manual adjusting processes
- Nanometer resolution and displacement up to 10µm
- Temperature sensor
These high force piezoelectric actuator are designed with stacks of discrete piezo disks made from “hard” PZT formulations. They are encased and preloaded to handle high push/pull forces. A variety of models with piezo ceramics diameters up to 35mm are available for different load requirements.
Custom actuator designs with larger travel ranges, higher forces or faster response, as well as non-magnetic versions are feasible.
Applications: These piezo actuators provide high forces and wide temperature ranges: some models up to 200 degrees C. They are used in high-performance optics and laser applications, precision machining, and downhole applications.
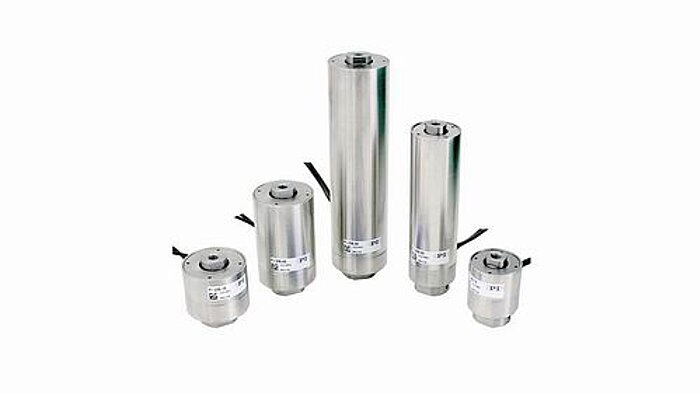
P-216/P-235 High-Load Stack Actuators
Preloaded, High Force
- Up to 180µm motion
- Pushing forces to 30,000N
- Pulling forces to 3500N
- Closed-loop for high accuracy
- Sub-millisecond response
- Sub-nanometer resolution
These piezo stacks and chips are manufactured based on multilayer cofiring technology at PI’s piezo ceramics division PI Ceramic. The patented design comprises an all-ceramic outer layer of the actuator, which acts as insulation making them more durable. The lack of conformal coating is an advantage in high vacuum applications.
Hermetically sealed versions with inert gas filling can be used in harsh environments.
Custom actuator designs with larger travel ranges, higher forces or faster response, as well as non-magnetic versions are feasible.
Applications: Piezo actuators provide high forces, unlimited resolution in the sub-nanometer range and are ideal for OEM applications in biotechnology, nano-dispensing, microfluidics, valve control, fast switching and nanopositioning, optics, medical-devices, life-sciences.
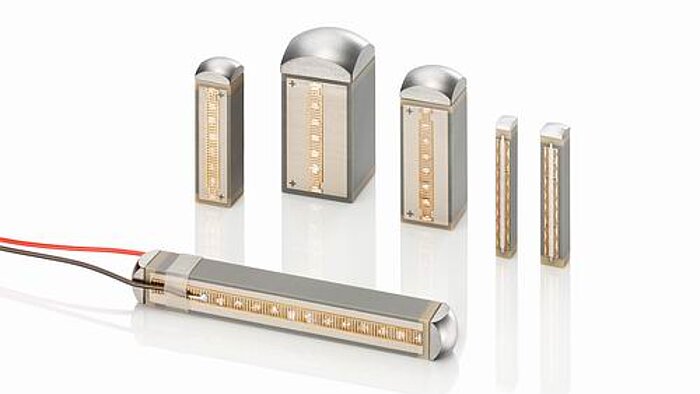
P-882 – P-888 PICMA® Multilayer Piezo Stacks
Mars-Rover Tested
- 9 to 30µm travel, 2x3 to 10x10mm cross sections
- Polymer-free cofired stack design
- NASA/JPL tested: 100 billion cycles
- Used in the Mars Rover Discovery
- Patented ceramic-encapsulation
- Large operating-temperature range
- High humidity resistance
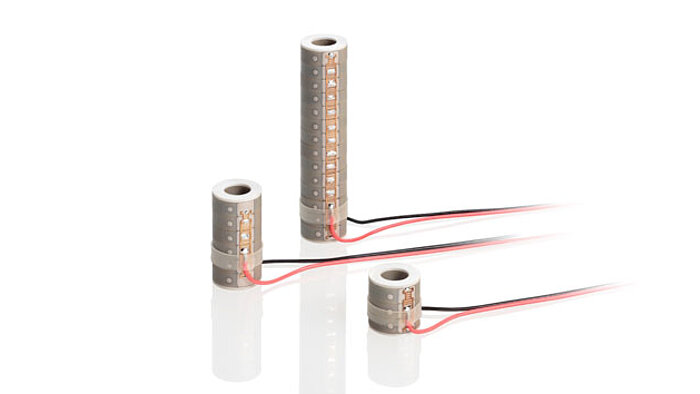
P-080 Tubular Piezo Stacks
Multilayer, Segmented
- 5 to 25µm travel
- Tubular stack (axial extension)
- Sub-nanometer resolution
- Aperture for optical applications or preload
- High force generation to 800 N
- Fast response, for dynamic operation
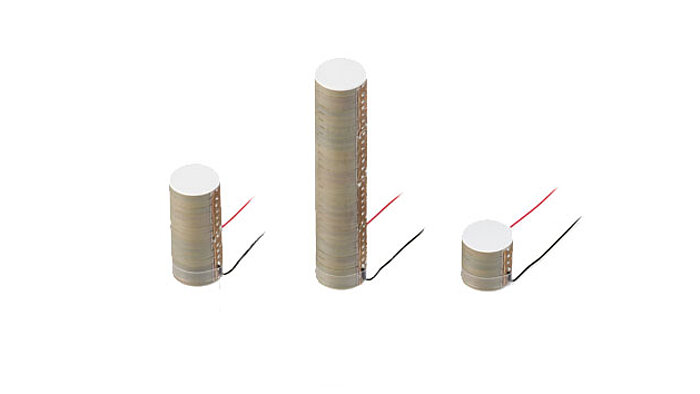
P-088 Piezo Stack Actuator
Multilayer, Segmented
- 14 to 70µm travel
- High force generation to 7500N
- Fast response, for dynamic operation
- Sub-nanometer resolution
- Segmented multilayer design
- Ceramic encapsulation for extended lifetime
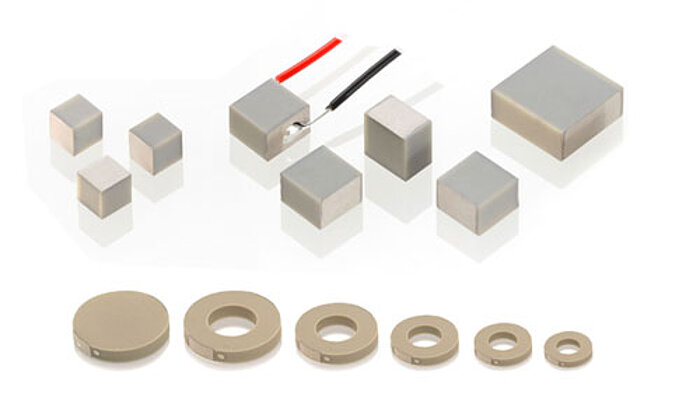
Piezo Chip Actuators
Annular, Circular, Square
- Ultra-compact, from 2x2x2mm
- High Curie temperature
- Manufactured from PIC materials (PIC 252)
- Ideal for dynamic operation
- Sub-millisecond response / Sub-nanometer resolution
- UHV compatible to 10-9 hPa
- Superior lifetime
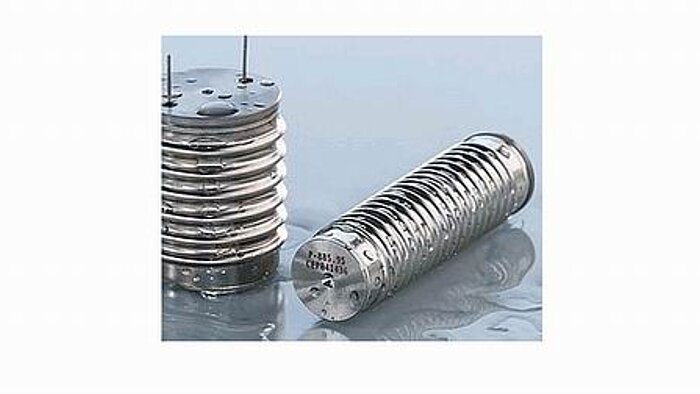
P-88x Waterproof Piezo Actuator
For Harsh Environments
- Waterproof and oil-proof
- Cofired monolithic piezo stacks
- Hermetically sealed steel container
- Inert gas filling
- Optional heat conducting compound filling
- Superior lifetime
PICA piezo stacks are built from discrete piezo disks made from “hard” PZT formulations. They are available in a large variety of diameters and shapes for different load requirements and applications. Discrete actuators are well suited for customizations, even in smaller quantities. They can operate under temperature ranges, some models up to 200 degrees C. They are used in high-performance optics and laser applications, precision machining, and downhole applications.
Crystalline piezo materials can provide extremely high linearity which is an advantage for high dynamics applications – no need for feedback sensors and closed-loop circuitry. The improved linearity comes at the expense of displacement.
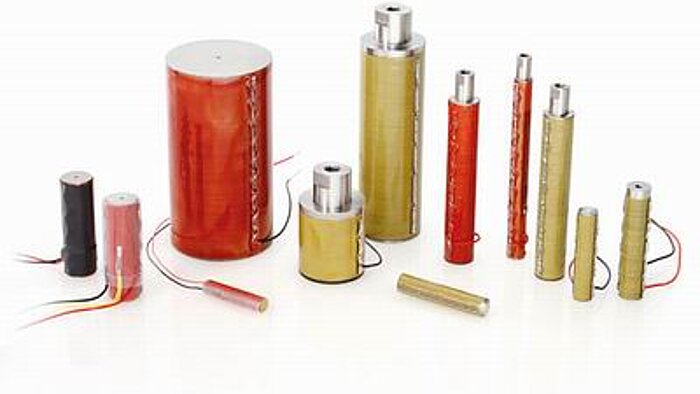
PICA Power High Force Piezo Stacks
Discrete PZT Actuators, Ø7-56mm
- 5µm to 180µm travel
- High force generation to 80kN
- High temp option to 200°C
- Extreme reliability >1 billion cycles
- Proven and flexible design
- Sub-nm resolution, Sub-msec response
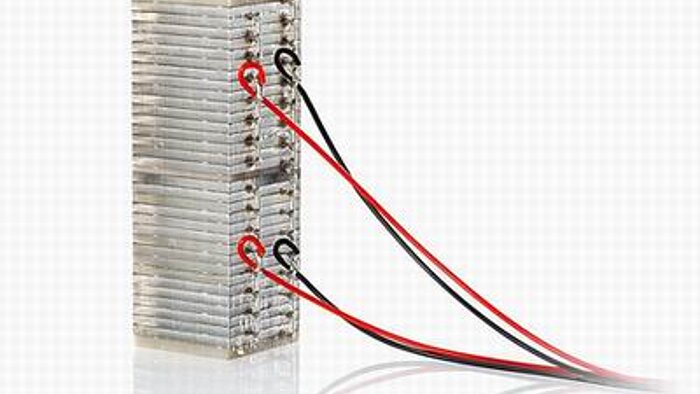
P-405 High Linearity Piezo Stack
High Dynamics, Open Loop
- Lead-free, highly linear crystalline material
- Provides linear motion in open loop – ideal for high dynamics applications
- Low electrical power consumption
- Minimal length tolerances
Piezo Benders, Bimorph Transducers
Multilayer, Steel-Ceramic and Laminated Transducers for Extra Flexibility
Bimorph, unimorph and multimorph bending mode actuators make use of different layers of active and non-active materials. Lateral motion created by the d31 effect is amplified multiple times. The advantage is relatively large amount of motion (100’s of microns to millimeters) in a very compact, low profile package. With the extended motion comes a trade off in force and stiffness.
PI manufactures multilayer (low voltage) and discrete bimorph bender actuators in different standard and custom shapes.
DuraAct® patch transducers are laminated and provide great flexibility with bending radii to 12mm. They can be used as senor in structural health testing and as actuator at the same time. Another version based on longitudinally oriented multilayer piezo ceramics (DuraAct Power) uses the high-efficiency d33 effect with reduced operating voltage.
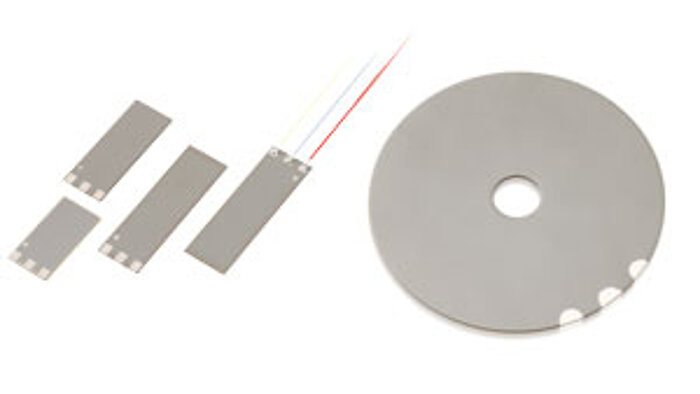
PL112 Multilayer Piezo Benders
Circular, Rectangular, Low Voltage
- 200µm to 2mm deflection
- Disk & rectangular shape, aperture
- Multilayer piezo => Low drive voltage (±30V)
- Fast response (<10 Millisecond)
- Nanometer resolution
- Ceramic insulation for extended lifetime
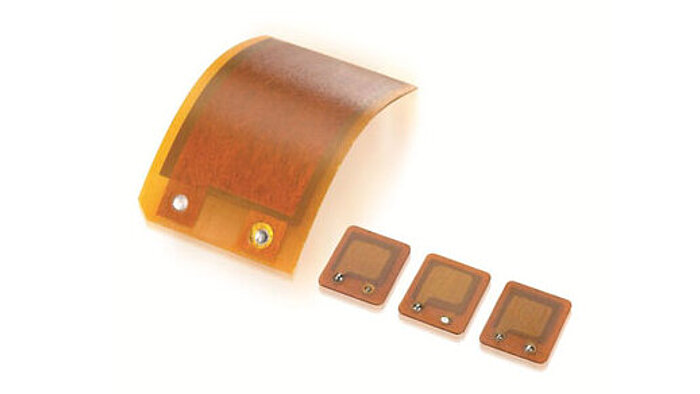
P-876/8 DuraAct™ Flexible Piezo Transducer
Sensor and Actuator
- Patch transducer can be used as actuator, sensor or energy source
- Highly formable ceramics
- Can be applied to curved surfaces
- Customized solutions on request
- Cost-effective
Traditional PZT tube actuators are often used in scanning microscopy applications, fiber-optics, and nano-dispensing. When a voltage is applied, the tube shrinks radially and axially proportional with the voltage. Due to the low mass they are very fast, but cannot support high loads.
For high-load applications and when axial motion is required, the P-080 multi-layer tubular stacks are recommended, or the PICA Thru discrete tubular stack family, for extra high loads.
PICA Shear actuators can also be used in lateral scanning applications. They are more robust than scanner tubes and come in single axis to XYZ configurations.
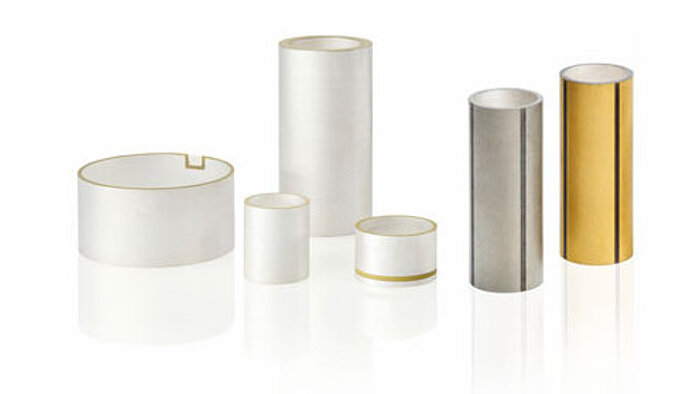
PT120 – PT140 Piezo Tubes, Scanners
From <2mm Diameter
- Miniature size option
- XYZ-scanner option
- Wall thickness as small as 0.3mm
- Sub-nanometer resolution
- Large diameters to 80mm
- Based on d-31 piezo effect
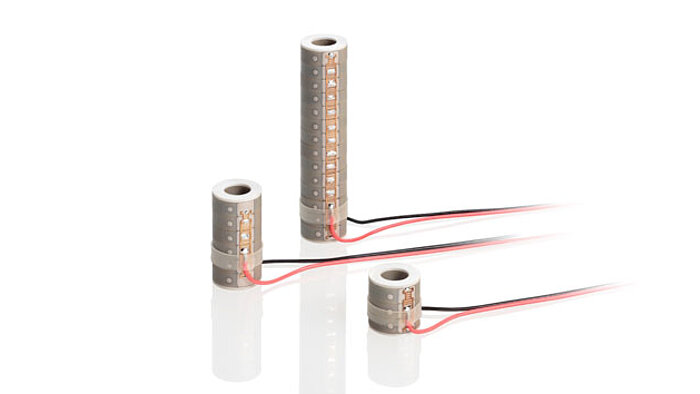
P-080 Tubular Piezo Stacks
Multilayer, Segmented
- 5 to 25µm travel
- Tubular stack (axial extension)
- Sub-nanometer resolution
- Aperture for optical applications or preload
- High force generation to 800 N
- Fast response, for dynamic operation

P-010.xxH – P-025.xxH PICA Thru Discrete Tubular Piezo Stacks
Axial Extension, High Force
- To 80µm axial motion
- Large cross-sections for high force
- Extreme reliability >1B cycles
- Custom geometries
- Sub-nm resolution / Sub-msec response